Crunch time for Phoebus
Launching things into space is hard. Aside from the engines and software, orbital calculations and the launch pad, the tanks that hold the fuel are a masterful example of engineering in their own right – and ESA will soon be testing the next generation of rocket tanks: Phoebus.
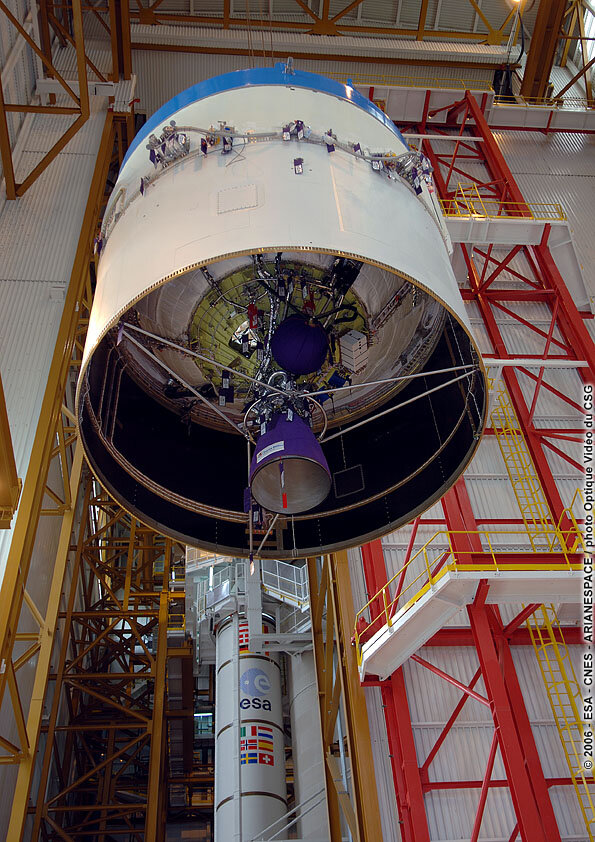
Consider this: European rockets often run on liquid oxygen and liquid hydrogen, these are great propellants, but in liquid form they must be kept at extreme temperatures below -200°C. Rocket tanks must keep these superchilled liquids cool, while also weighing as little as possible.
Hydrogen has a couple of other complications up its sleeve, as it is the smallest molecule in the Universe and small things are hard to keep contained, a hydrogen fuel tank needs to be one of the most leak-tight containers humans can make. Hydrogen gas is also very light, large volumes are therefore needed to store relatively small amounts of gas, again complicating the task of keeping the tanks lightweight. Stored in liquid form, the fuel tanks are pressurised to ensure the fuel reaches the engine at the correct pressure and temperature, so not only do the tanks need to be leak-tight and insulating they also need to be strong.
Liquid oxygen has an extra property that makes it hard to store: it is highly reactive and will quickly corrode many materials. Designing and building the right tank for a rocket is no easy feat, and it gets even more complicated during launch. On ignition of a rocket engine and liftoff the rocket is subjected to an intense blast, compressing and shaking each component, and the fuel tanks get the worst of it as they hold liquids that slosh around inside.
Carbon-plastic fantastic
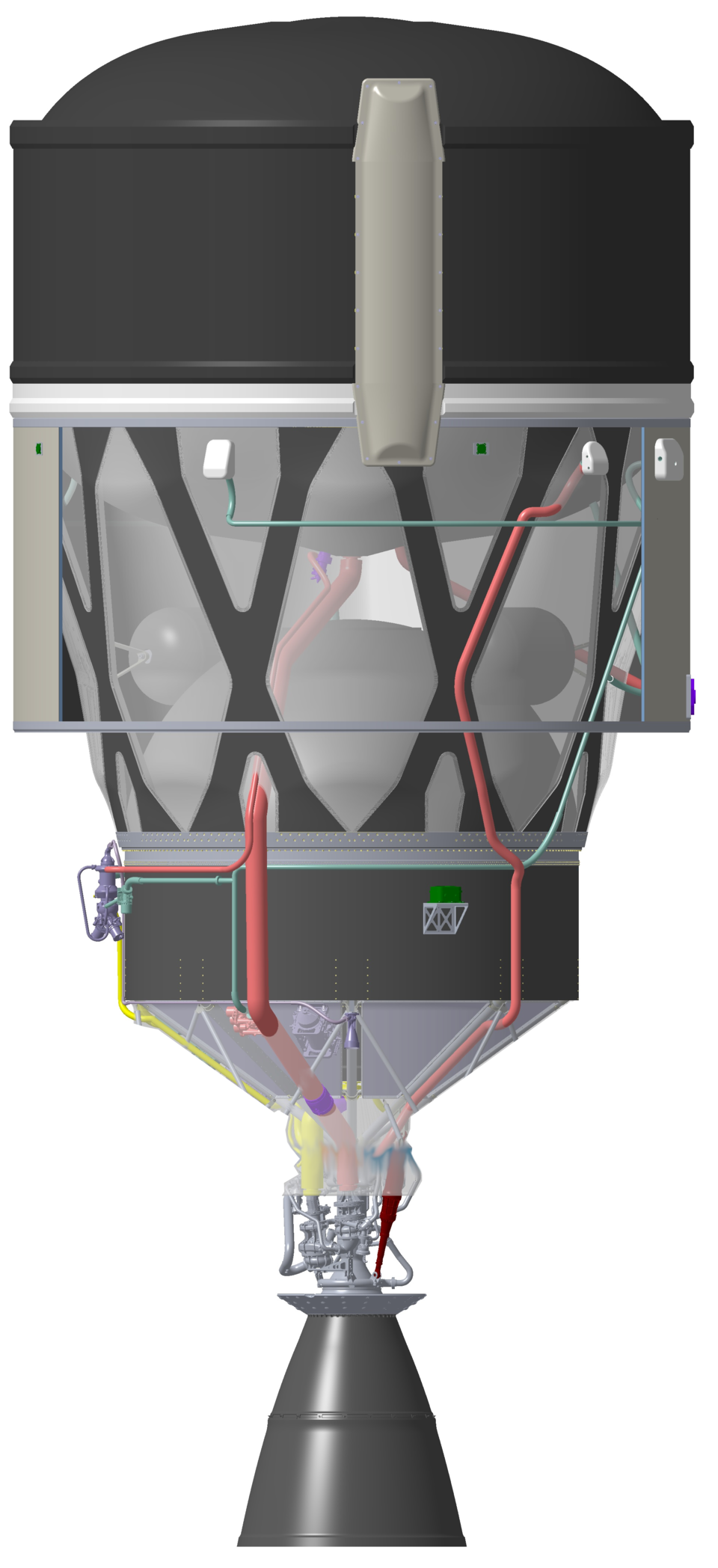
ESA’s Phoebus project is looking to carbon fibre-reinforced plastic for the next generation of rocket fuel tanks. Carbon fibre materials have taken the world by storm as they are extremely lightweight and strong, but so far they have not been able to be made suitably leak-tight for storing liquid hydrogen, nor liquid oxygen due to its reactivity. European teams at ESA, MT Aerospace and ArianeGroup have now overcome both these limitations by using new manufacturing technologies, as well as state-of-the art design methodologies and fine-tuning the plastics chemistry.
Phoebus is a carbon-fibre reinforced-plastic fuel tank demonstrator that is built from the ground up using layer-by-layer manufacturing. This technique and the innovative design allow engineers to construct a unique shape that suspends the fuel tank inside a supporting frame, with an insulating air gap in between, solving many of the problems above in one additive swoop. Light-weight, strong, leak-tight and non-reactive, last week a key element of the Phoebus project passed its test-readiness review and was given the go-ahead to proceed for testing, where a 2-m-diameter model oxygen tank will be tested as if it were really flying. A similar scale hydrogen tank will be tested next year, ahead of the testing of a full-scale structural demonstrator of a complete upper stage in 2025.
“The physics, chemistry and construction techniques behind this project are mind-boggling,” says Kate Underhill, ESA’s lead engineer on the project. “When we started Phoebus, the risks were high and the fact that the project has reached this stage is thanks to the huge commitment and know-how of teams involved at ESA, MT Aerospace and ArianeGroup working together as one.”
Pushing and pulling
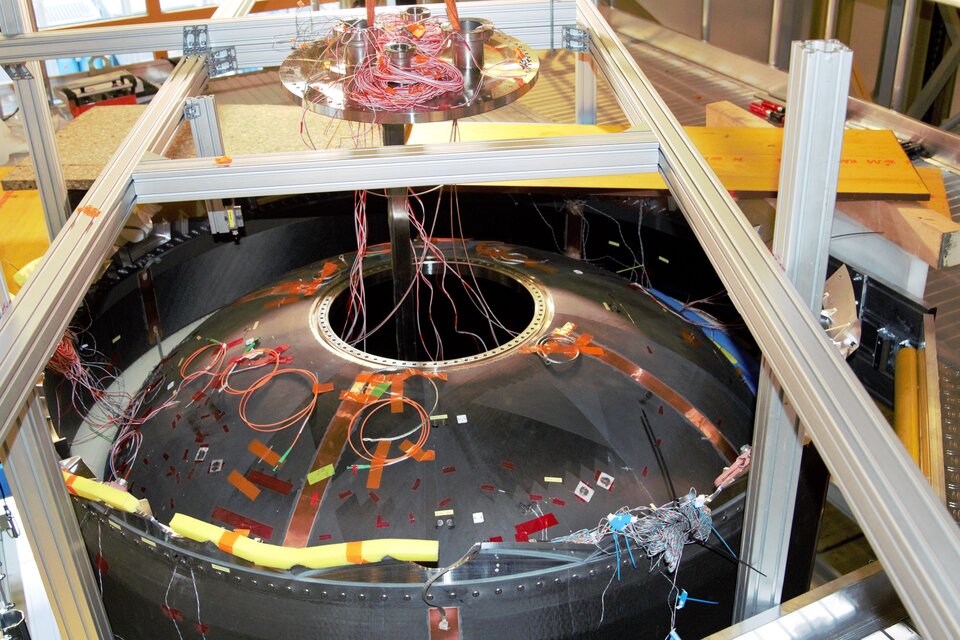
The first step for testing is pressurisation with nitrogen and then helium – a gas used to help identify if there are any leaks in the tank.
If Phoebus passes this test, the next step will be to test with oxygen, “We will be moving Phoebus to a Rheinmetall military test site in Unterlüß, Germany,” says Kate, “we can test there because they are used to handling explosions… when working with liquid oxygen, if things go wrong, they go wrong very quickly!”
The final tests will be the most “testing” for the tank, where it will be literally pulled and pushed to simulate the loads of a rocket launch at MT Aerospace in Augsburg, Germany. The tank will be filled and pressurised with nitrogen during this test to fully simulate its condition during flight.