Tough tests no problem for carbon-fibre cryo fuel tanks
Lightweight but super-strong. Extremely rigid or flexible and springy. Corrosion-resistant and ideal for complex shapes. All of these benefits come from carbon fibre, and when performance matters it is probably part of the package. Tennis rackets, bicycles, racing cars and airliners are just a few products that rely extensively on this miracle material.

It’s no surprise that modern rockets also perform better thanks to carbon fibre. More formally known as CFRP – carbon fibre reinforced plastic – this mix of super-strong carbon fibres and the binding resin that holds them in place is a great way to reduce the mass of a rocket, and so increase the payload mass it can carry. Ariane 6 and Vega-C both carry CFRP payload fairings, and the body of the P120C solid-fuel rocket motor that serves as Ariane 6’s boosters and the first stage of Vega-C is one of the world’s largest single-piece CFRP structures.
But can CFRP go further, and replace the metallic structures in a rocket’s cryogenic fuel tanks? That is the objective of ESA’s Phoebus programme, which aims to produce upper stage tanks and structures in carbon fibre – and so far it is acing its tests.
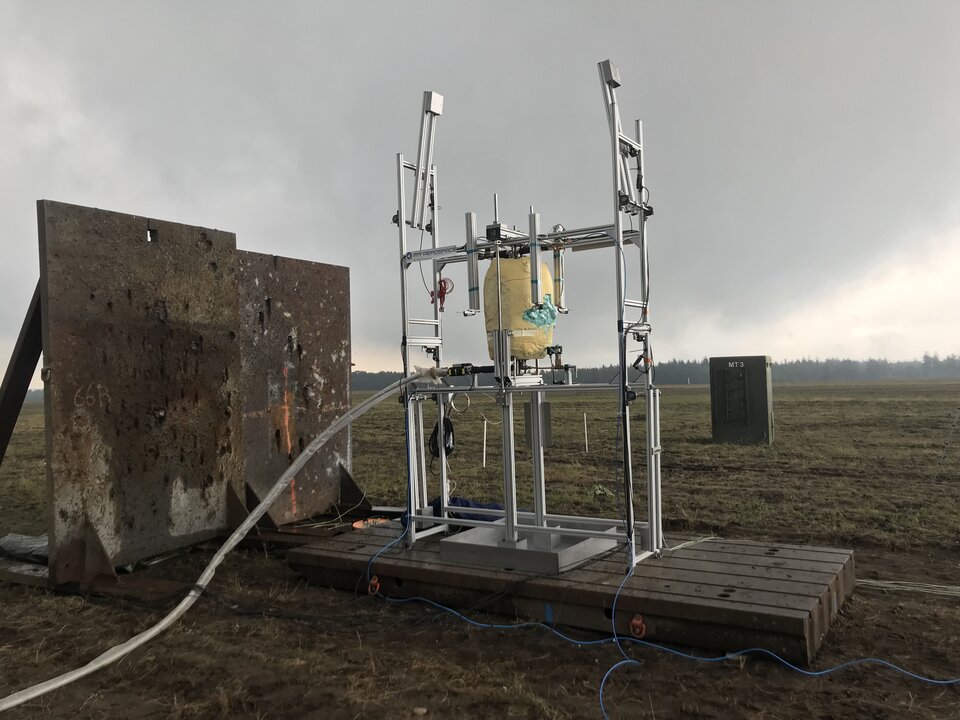
The mass reduction of an upper stage design based on Phoebus technology could in theory be enough to add around 1500 kg to the payload performance of a rocket like Ariane 6. That reduction comes from the inherent lightness of CFRP itself and of its great design flexibility, which enables the production of structures with novel shapes and fewer parts than metal counterparts. Production costs could also be lower.
After establishing that leak-proof CFRP tanks are in principle possible to manufacture, ESA through its Future Launcher’s Preparatory Programme contracted ArianeGroup and MT Aerospace in 2022 to go from early design studies to production and testing of cryogenic upper-stage tanks and structures.
Testing to destruction without explosion
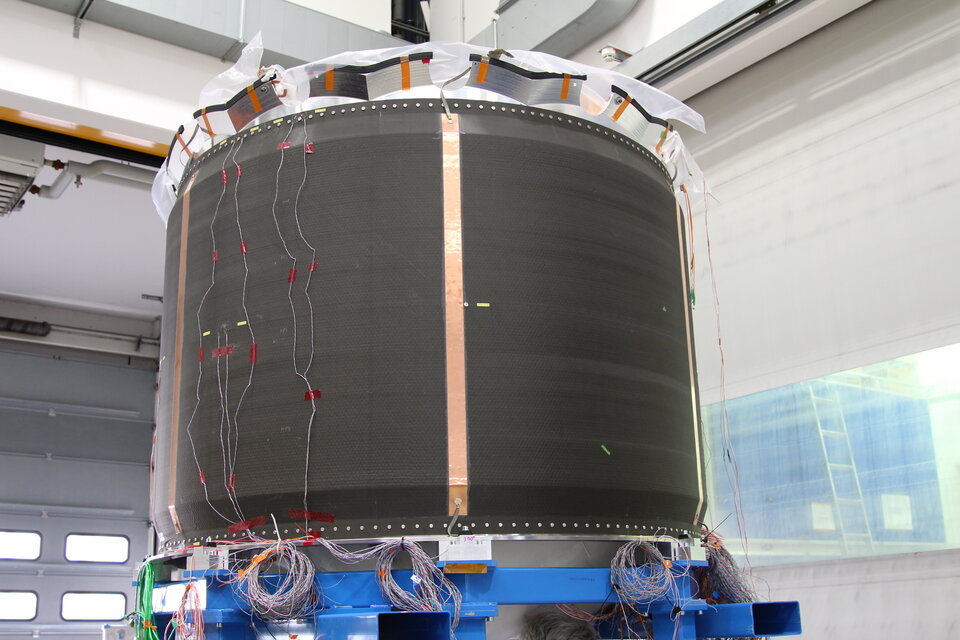
Phoebus has undergone a number of tests of progressive difficulty over the last weeks. The objective is to expose a mid-scale oxygen tank to thermal and mechanical loads that represent an actual launch. The first tests took place at MT Aerospace in Germany, which worked with ArianeGroup to design and manufacture the tank.
First up was a helium test in October: traditional metallic tanks are leak-tested with helium at room –temperature. If the CFRP tank could ace this test then that would both show that the basic concept for a ‘linerless’ leak-tight CFRP tank was possible but also release it for more intensive testing.
Next up was a cryogenic pressure test, also in October: the tank held it together while pumped full of liquid nitrogen at –196°C and under pressures of 13 bar (13 times the average atmospheric pressure on Earth at sea level), exceeding the stresses it will need to endure as a real rocket tank.
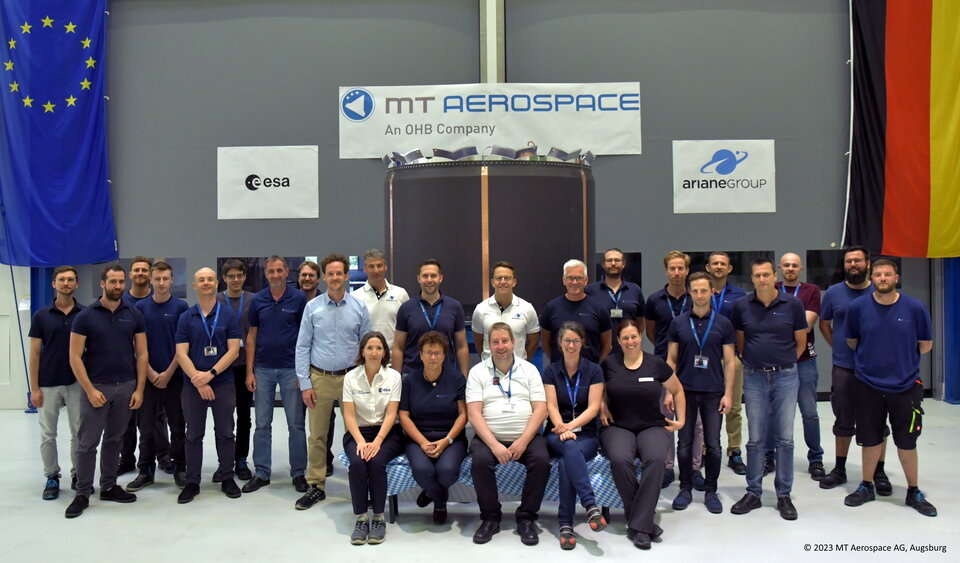
According to Kate Underhill, upper stage and propulsion demonstrators project manager in ESA’s Future Launchers Preparatory Programme, understanding the thermal behaviour of the CFRP tank during these cool tests is also important. Liquid hydrogen must be kept at –253° C or it boils to a gas, while oxygen is kept at –183° C in the tanks. CFRP is less thermally conductive than aluminium, so it takes longer for the tank to cool down and the temperature map of the tank is different – the parts that are not in contact with the liquid propellant are warmer than for a metallic tank.
As a bonus the Phoebus teams installed and tested a new way of measuring how much propellant a rocket tank contains as it burns away during flight. Using electrical capacitance tomography – exploiting the fact that liquids and gases conduct electricity differently – the tests have shown to be more accurate than current fill-level sensors and they could be incorporated into future rockets to reduce the amount of extra fuel that needs to be taken on board to cover for the inaccuracies of measurements.
Reaction oxygen
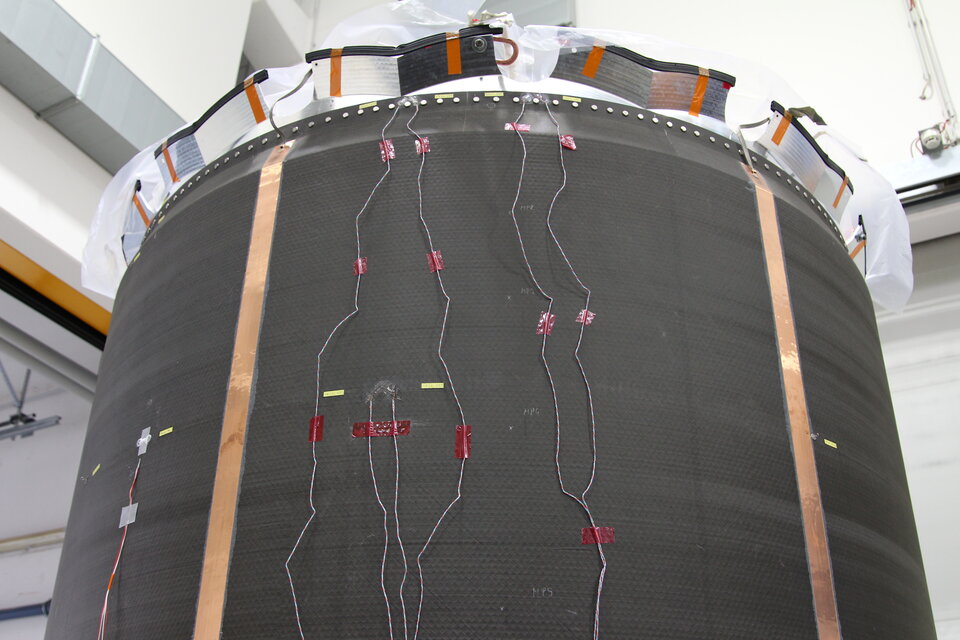
Then came the delicate part: a liquid oxygen test. Since this test can be dangerous if things go wrong, in December Phoebus was moved to the Rheinmetall military test site in Unterlüß, Germany – it is best equipped to handle a potential severe fire!
One of the biggest challenges with CFRP for fuel tanks is that carbon composite materials can be chemically very reactive with oxygen. As such, careful selection of the resins and fibre materials is required, whilst at the same time always keeping an eye on the potential leak-tightness of the selected resins and fibres.
“Phoebus is on a roll, the oxygen tank tests were a complete success, and the tank held it together perfectly – no fire, no explosion, I am a happy project manager.” says Kate, “Unfortunately the trials and tribulations for our little tank that can are not over yet. It has been shipped back to MT Aerospace where it will be pushed and pulled whilst also being pressurised, simulating the complex conditions of a launcher flight. And then after that the poor thing will be cut-up in the laboratory for detailed inspection.”
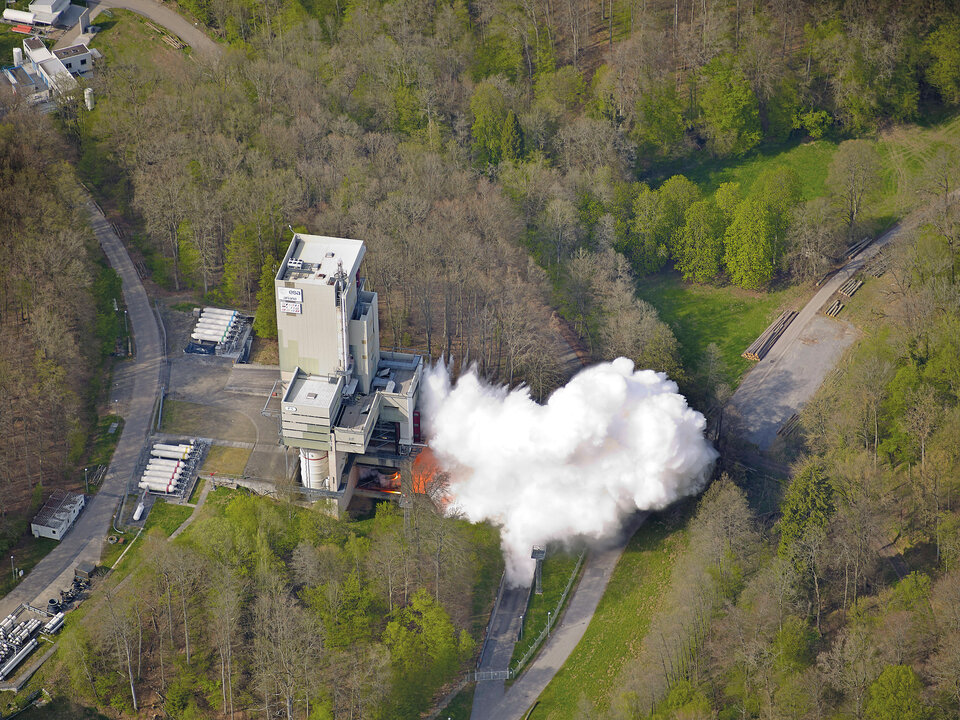
The next step for the oxygen tank concept is the manufacture of a full-scale version nearly four metres in diameter to match Ariane 6 dimensions. Subsequent testing with a CFRP hydrogen tank will take place at the German aerospace agency’s (DLR) propulsion testing site in Lampoldshausen. Before that, watch this space in 2024 as a hopefully equally plucky scaled-down version of the CFRP hydrogen tank will undergo a similar test campaign to confirm the full-scale design.
Kate adds that the ultimate goal is to use such tanks and structures in a new upper stage for Ariane 6 – lighter and cheaper than the existing stage with metallic tanks.