Speeding up the space industry with digitalised satellites
The ‘fit check’ is that moment in a launch campaign when a satellite is first attached to the launcher adapter that will cradle it on its flight to orbit. This is supposed to be a mere formality, but uncertainty is there in its very name: what if these two items, manufactured in different parts of Europe, don’t fit together as planned?
ESA’s Design 2 Produce initiative should make the fit check – along with many parallel test activities in the current Assembly, Integration and Testing phase of a space mission’s life – obsolete. Design 2 Produce involves transferring the ‘Industry 4.0’ digitalisation approach, growing in popularity in terrestrial manufacturing, to cut the cost and schedule of space missions.
Industry 4.0 is changing the manufacturing process in various ways, including a single, seamless digital data cycle to link key disciplines from design to production, automated inspections, embedded sensors to give an authoritative, ongoing overview of product status and augmented reality to guide integration and testing.
It starts with replacing reams of documentation produced by space projects today with digital models that can be worked on directly – to ‘see’ the satellite directly, from an early stage, rather than imagining it based on words and numbers.
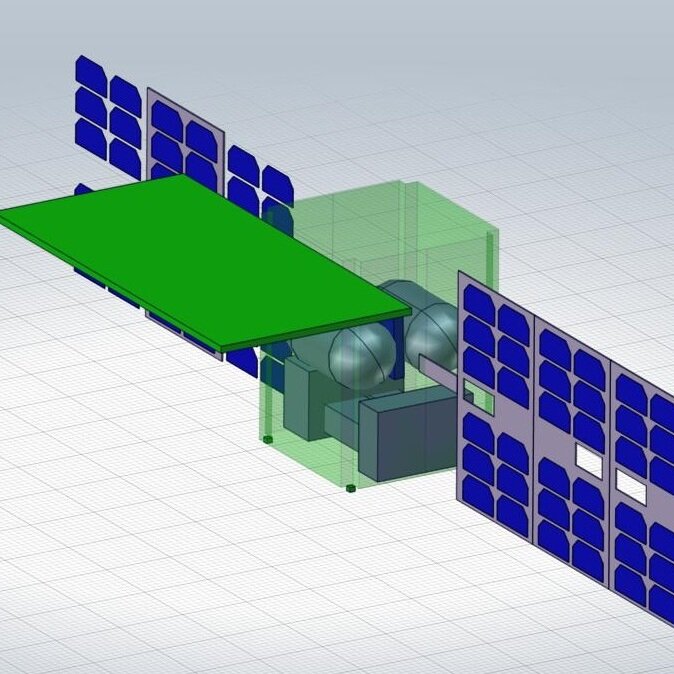
“Key to the Design 2 Produce approach is the creation of an extremely high-fidelity digital model of the space system, to do more preparation upfront,” explains ESA system engineer Ilaria Roma.
“This model is centred around a hub that connects all stages of the design and production cycle, not only in terms of engineering but also management and procurement, requirements formulation and so on.
“The power of digital is that everyone is working with the same information, so there are no inconsistencies or other surprises to be resolved in the integration stage. And the digital models are so good that authoritative simulated testing can take place in advance of physical manufacturing in areas such as thermal engineering.

“We won’t need all the tests we perform now, because any anomalies will be identified at earlier stages. For instance in the past, there have been missions where panels have been placed too close together so there isn’t enough room for an operator to use a screwdriver. We can get rid of occurrences like this, and operators can be trained well in advance with the digital model, to be perfectly prepared and able to work faster and more carefully.”
Another aim of Design 2 Produce is to harvest as much data as possible throughout the design and manufacturing cycle, through embedding sensors throughout the satellite. The resulting data can then be analysed by artificial intelligence and machine learning to identify improvements in design and manufacturing processes on an ongoing basis.
These sensors can also be put to use during satellite testing – at the moment test engineers must place their own sensors inside, then remove them once each test is done.

Finally, Design 2 Produce also involves the adoption of virtual and augmented reality on the factory or test centre floor, guiding engineers in their actions using the digital master model of the satellite.
These techniques have been pioneered by terrestrial aerospace and automotive manufacturers, and have also been adopted by some parts of the space sector already.
“Manufacturers of satellite mega-constellations, producing hundreds of identical satellites for planned service in low-Earth orbit have made use of digitalisation,” adds Ilaria.
“They’ve had to, in order to achieve the necessary per-satellite cost and time constraints. What we want to do is transfer these batch production techniques to the kind of mission ESA typically oversees, which is a single high-performance spacecraft. We’d be producing way less, but we think by adopting a stepped approach we can still show many benefits.”
As a cross-cutting initiative, Design 2 Produce involves coordinated projects run through ESA’s different technology programmes, starting with its Technology Development Element for early proof-of-concept, progressing through the General Support Technology Programme, for mature flight hardware.