Applying a long-term perspective: Laurent Pambaguian interview
Laurent Pambaguian of ESA’s Materials Technology section, an expert on the metallic materials and processes employed to build space missions, is advising Clean Space on additive manufacturing, identified as a high potential green technology.
How do you sum up Clean Space?
Clean Space is applying a long-term perspective to the space business. We will measure the environmental impact of our activities and then work to reduce this impact. To do so, we aim to develop advanced cleaner technologies and also reduce the risk of collision in orbit by reducing the production of debris and removing debris from space . Through smart thinking, we should also boost the competitiveness of Europe’s space industry.
How did you get your start in the space field?
I started through working on material technologies, designing and testing materials that were potentially ‘enabling’. This, in space terms, means they had the potential to extend the in-service maximum temperatures or else to save a lot of mass, or extend the mission lifetime…
I began working in the space field in the late 1980s, and am still in it today. If we were able to make space missions out of a single material, I’d be instantly out of work, but different materials have different strengths and weaknesses. So it becomes a matter of identifying which materials and processes can be used for which application, and whether they can be used in combination without ill effects.
What is your role within Clean Space?
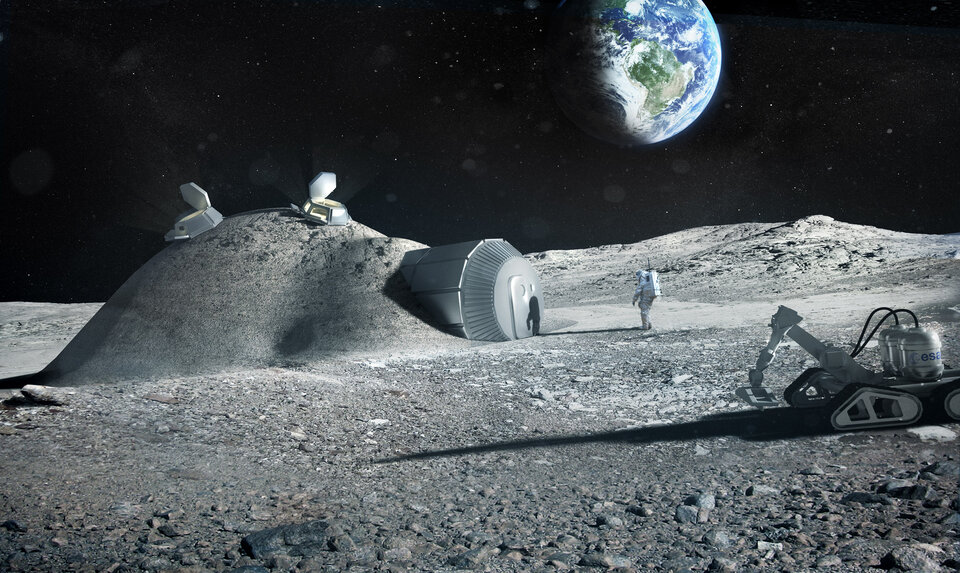
For Clean Space I’m advising on Additive Manufacturing, one of the green technologies identified as having a very high potential. With conventional machining we remove more than 70% of a block of material to make a part, with limited capacity for not downgrading the recycled waste. With AM the part being designed is built up gradually by stacking thin layers of material on top of each other. In theory there is no wasted material, much less energy required and access of the cutting tool to surplus material is no longer dictating the design rules – although we are finding it can be a little more complicated in practice…
The real challenge is going to be changing our way of doing business to take the maximum advantage from such new developments. Being able to move straight from design to production with much fewer manufacturing steps is potentially revolutionary, but we’ll need to reorganise our way of working – and thinking. The space industry tends to stick with the old ways of doing things over the past half a century or more because any new development will need to be qualified for space and that is costly.
How did your involvement in Clean Space begin?
My involvement in Clean Space goes back to initial sustainability studies. In the last few years I took place in a Concurrent Design Study called ‘Ecosat’, in which a team looked for ways to reduce the carbon footprint of a space mission. The exercise proved valuable – highlighting how little we understood the impact of our daily activities, and how much there was to learn.
From my view point, Clean Space is something we need to do: looking at the space business with a long-term perspective. It is a proactive initiative looking at what we have done wrong in the past and how to correct this, while also learning how to do better in future, by monitoring our overall activity with the same accuracy and rigour that we apply to data from ESA missions.
How do you see Clean Space evolving in future?
I don’t see Clean Space as an isolated initiative so much as the first in a series of ‘Clean…’ initiatives, as a model for other industries to become smarter. It should be like the ‘ISO management’ standards, being considered as a continuous improvement exercise.