Advanced Injectors for Chemical Rockets Inspired by Ink-jet Printing Technology
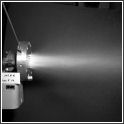
Injection is a key process realising feedback couplings of the combustion chamber with other engine components. In Liquid Rocket Engine systems, propellant injectors and feed manifolds are used to feed the propellants into the combustion chamber. The injectors atomize the propellants as much as possible and spray them into the combustion chamber in a pattern that helps the propellant to mix and burn. Their function is to provide a pressure drop to prevent pressure pulses from moving up into the feed system.
The performance and hardware integrity of liquid rocket engines is greatly influenced by the propellant mixing near the injector. In an injector the pattern, sizes, distribution and types of orifices deeply influence the combustion behaviour as do the pressure drop, manifold geometry or surface roughness in the injector orifice walls. The evaluation of the flow characteristics near the injector is thus very crucial in the advanced liquid rocket engine design.
Injection is a key process realising feedback couplings of the combustion chamber with other engine components. In addition to its main function of injecting propellant and preparing a combustible mixture, a liquid-propellant injector simultaneously acts as a sensitive element that may generate and modify flow oscillations because of its intrinsic unsteadiness and interactions with the combustion-chamber and feed-system dynamics. Injectors always function in nonsteady flow environments and are therefore considered as a dynamic component of an engine, as they may generate and modify flow oscillations.
In a drop-on-demand inkjet printer, ink fills a chamber and a drop is ejected through a nozzle on demand. The technology for the ejection mechanism is based on the use of piezoelectric materials. The chamber walls are piezoelectric crystals. When current is applied, the crystal deforms, forcing a droplet of ink from the nozzle. The ejection chamber and the nozzle are built with microtechnologies and due to very small dimensions.
Preliminary assessments indicated that, if this ink-jet technology is applied on small bipropellant rockets and hybrid rockets, one can expect an improvement of the propellants atomisation rate before the injection in the chamber of combustion thus reducing the time, an increment in the ratio surface area to volume to promote evaporation thus the mixing process by transforming liquid in fine droplets as well as a reduction in the response time to rapidly changing inputs, e.g., rapid throttle movements. However, detailed assessments needed to be performed at greater depth in order to determine a precise prediction of injector performance and interactions with the combustion-chamber and feed-system dynamics, so that the concept can be reliably compared against competing solutions.
In collaboration with European academia, the ACT conducted a study on the feasibility of the injectors for chemical propulsion systems. The main objectives of this study were:
- Evaluate the applicability of the Ink-jet technologies on injectors design for chemical rockets in term of mechanical properties at high working temperature and thermal cycling.
- Assess possible showstoppers, benefits and drawbacks of using this technology for aerospace propulsion systems (including the identification of suitable materials and propellants).
- Determine a suitable piezoelectric injector configuration and estimate the spray characteristics (in terms of droplet mass and size distributions) and the injector performance
- Perform an analytical study in order to evaluate the interactions of the piezoelectric injector configuration with the combustion chamber and feed system dynamics.
- Identify critical issues associated with the injector configuration, e.g. structural failure under mechanical pressure, vibration and acoustic noise environments, fatigue failure and reliability
References
- C.R.Peterson, P.G.Hill. Mechanics and Thermodynamics of Propulsion, Addison- Wiley, 1992.
- Lefevre A. H., Atomisation and Sprays, Hemisphere Publishing Corporation, New York, 1989.
- Barazov, Yang. Liquid-Propellant Rocket Engine Injector Dynamics. Journal of Propulsion and Power,Vol. 14, No. 5, September -October 1998, pp 797-806.
- Cheng G., Farmer R. Development of Efficient Real-Fluid Model Simulating Liquid Rocket Injectors Flows. 39th AIAA/ASME/SAE/ASEE Joint Propulsion Conference and Exhibit 20-23 July 2003, Huntsville, Alabama, AIAA 2003-4466.