ESA seeks cleaner means of ‘cooking’ composite satellite parts
Modern satellites and other space hardware have something in common with top-of-the-range boats or Formula 1 racing cars: they’re often as much ‘cooked’ as they are built, composed of advanced composites that are rigidly set in place. Now ESA is looking into greener, more sustainable alternatives to producing these materials.
Composite materials such as carbon-fibre-reinforced polymer have become a cornerstone of modern spacecraft production.
Composite components, with optimised strength and rigidity, are manufactured in a standardised manner, typically with ‘wet-layup’ – where composites are laid down in a mould – followed by ‘vacuum bagging’ – where a bag layer is applied from which all air is then extracted so this bag precisely hugs the composite surface – and then ‘autoclaving’ where composites are cooked or ‘cured’ inside high-temperature, high-pressure chambers.
The additional materials used to manufacture and process such components have a significant environmental impact, and typically cannot be recycled.

But because ESA is in the process of studying its environmental impacts with the aim of reducing them, a new study intends to investigate alternative approaches towards sustainable, green ancillary materials for composite structure manufacturing.
Indeed, in a current composite manufacturing process a wide variety of ancillary materials are included, typically:
– Peel piles are woven fabrics generally applied as the last material in the composite laminate sequence. Usually made of polyamide (nylon) or polyester fibres, they are designed to be peeled from the surface following cure to leave a clean and contaminant-free textured surface.
– Release films are used to separate and release the laminate from the vacuum stack following the composite cure.
– Vacuum bagging films are used to seal the whole of the composite laminate to the tooling surface, with a standard vacuum applied in order to apply atmospheric pressure to the component. Typically nylon-based, these films can stay at a standard one-atmosphere cure cycle at the chosen temperature or have their pressure increased in the autoclave.
– Tapes are used in a variety of applications: sealant tapes (typically rubber products) provide an integral seal to the tool with flash/release/shrink tapes (typically polyester) as assembly aids or to mask areas.
– Mould release agents, such as Teflon-coated glass fabrics, release waxes or agents.
– Breather or bleeder fabrics allow the removal of trapped gas and absorb any excess resin, typically polyester-based.
– Solvents for surface cleaning and preparation.
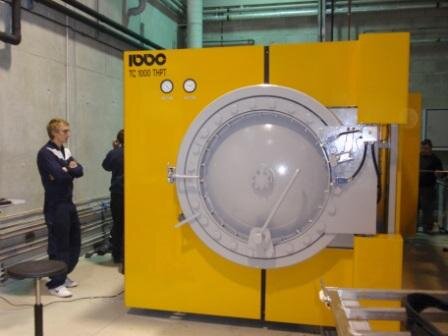
Accordingly, ESA has issued an Invitation to Tender to investigate sustainable, green ancillary materials for structure manufacturing.
Alternative materials with a lower environmental impact will be considered during the activity.
For more information check the invitation to tender package, accessible via ESA’s Electronic Mailing Invitation to Tender System (EMITS).