Spin and bones
We all have skeletons beneath our skin, so subtracting that skin is a good way to understand how the human body reacts to a ride on a fast-spinning centrifuge, experiencing ‘hypergravity’ in the process.
An ESA project is applying an ultra-detailed computer model of the human skeleton and musculature to test techniques to protect astronauts against the gradual wasting effects of weightlessness.
The AnyBody Modelling System, developed by the Denmark-based AnyBody Technology company, is the world’s most detailed ‘musculo-skeletal’ model of the human body, incorporating more than 100 bones and 910 muscles.
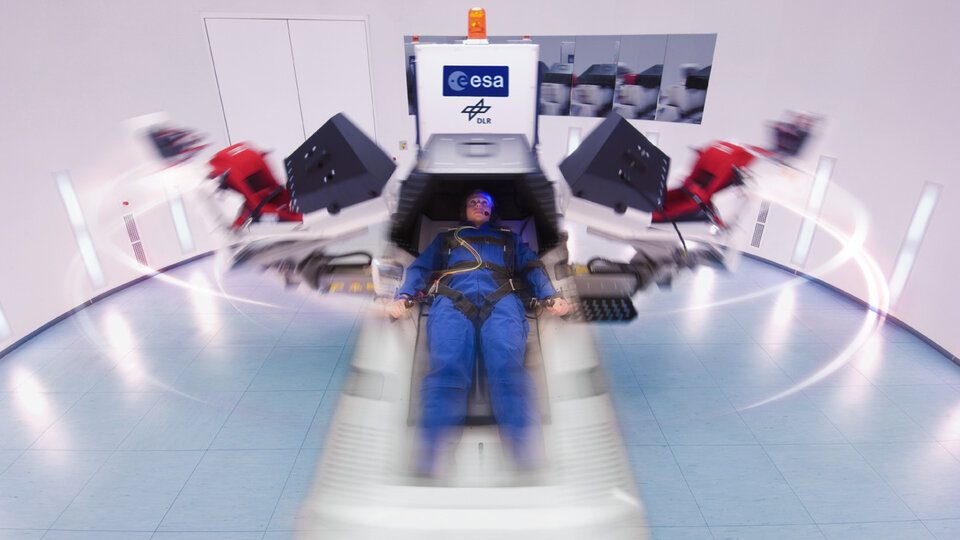
The model is in widespread use by academia, healthcare and industry – with users ranging from BMW to Zimmer – for testing new products: how easy would they be to use in practice, and what muscle forces are needed to manipulate them?
ESA is looking into applying the model to test the designs of ‘countermeasure systems’ for astronauts in space – exercise techniques or machines aimed at reducing bone and muscle loss while living in a weightless state. Astronauts in orbit can lose more than 1% of bone mass per month with muscle mass shrinking by up 5% weekly.

"But it can be difficult to assess the effectiveness of countermeasures down on the ground," explained Arnaud Runge, a biomedical engineer overseeing the project for ESA.
"So ESA began a pilot project to apply the AnyBody model to computer-aided design models at an early stage of their development."
The project assessed a prototype treadmill design for use in microgravity as well as an actual piece of hardware, the ESA-developed Short-Arm Human Centrifuge, operated by DLR’s Institute of Aerospace Medicine.
This research was supported through ESA’s General Support Technology Programme, intended to convert promising engineering concepts into a broad spectrum of mature products.