Breaking boundaries: A 3D Printer taking space manufacturing beyond limits
In brief
The groundbreaking IMPERIAL 3D printer developed for space manufacturing has overcome traditional limitations by using a temperature-controlled conveyor belt, enabling continuous printing of large parts in microgravity. The success of the ground-based prototype and collaborative efforts set the stage for testing the IMPERIAL printer in the microgravity environment of the International Space Station, marking a significant leap in in-space manufacturing capabilities.
In-depth
In a leap towards the future of space manufacturing, a TDE activity has developed the IMPERIAL 3D printer, a groundbreaking technology designed to print parts much larger than the available printer building volume. Overcoming the limitations of conventional 3D printing processes, this innovation holds the key to reshaping how structures, tools and spare parts are produced for future long-term manned missions.
IMPERIAL has been crafted with extraterrestrial manufacturing in mind, paving the way for astronauts to print essential components as needed during their missions.
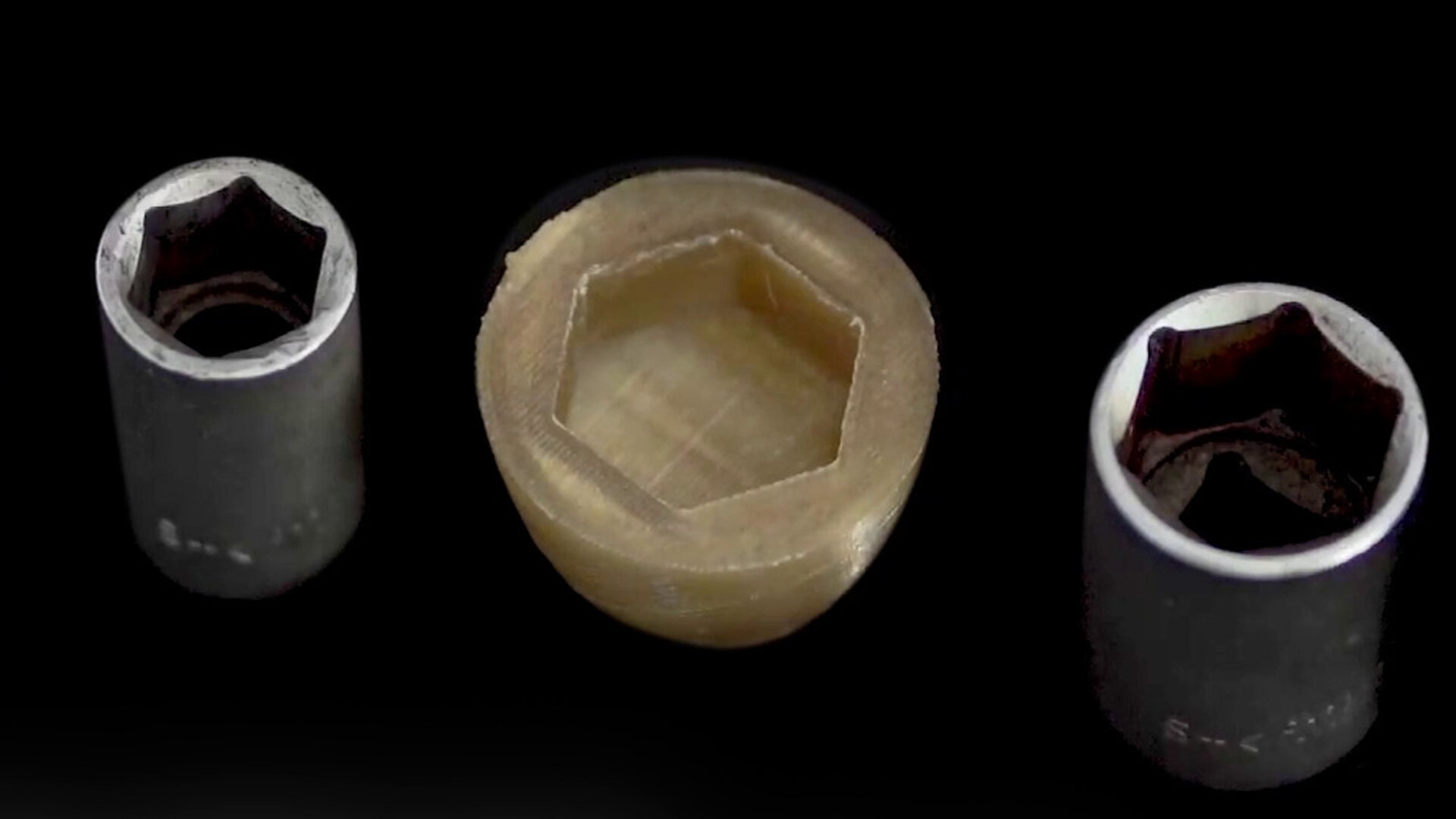
Access the video
The IMPERIAL Printer, was borne out of a previous ESA activity, called MELT and stands out due to its ability to overcome a significant limitation of conventional 3D printers while meeting the fabrication requirements of the International Space Station (ISS). One of the key improvements on the previous printers is its ability to print continuously without stopping. Traditional printers are confined by the size of their interior, meaning they can only print parts smaller than the printing volume offered by the printer chamber. IMPERIAL introduces a game-changing feature: a temperature-controlled conveyor belt. This belt allows parts to be printed without any limitation in one direction exploiting the conveyor belt mechanism and revolutionising the possibilities for creating structures in space. In microgravity conditions, the need to wrap printed parts is eliminated as they will not fold, streamlining the manufacturing process.
“It can all be printed now. We are able to print functional parts, especially tools, and interface them with counterparts already onboard the ISS, we can process different materials, such as electrically conductive polymers for small CubeSat components and enclosing or the structure of very large items, such as telescopes. Now we can print anything which needs to withstand the harsh environment of space” explains Francesco Caltavituro, a space and systems engineer at OHB who worked on the project. “It can all be printed, especially if you want to use high-performance thermoplastics (PEI, PEEK and PEKK), this printer can handle them.”
With great advancements often come great challenges. High-performance polymers, chosen for their exceptional mechanical and thermal properties, became the materials of choice for in-space and on-planet printing using the IMPERIAL printer. The MELT printer laid the groundwork by developing a 3D printer capable of printing high-performances structural materials like thermoplastic polymers under ISS microgravity conditions, producing functional parts and standard mechanical samples successfully. Printing large parts for in-space construction introduces thermal processing challenges, particularly when using these demanding high-performance thermoplastics. To overcome this, the Industry Team under ESA guidance implemented a precise heating system to maintain a uniform temperature within the chamber and also outside it, along the conveyor belt mechanism, crucial for printing homogenous parts with materials like these, avoiding undesired shrinkage and warping. Additionally, the innovative approach of printing on a movable belt requires careful consideration in terms of quality estimation for the manufactured parts. The prototype breadboard built for the project encompasses various subsystems, including the core printing components, a thermo-mechanical housing based on the EDR Experiment Insert (EI) dimensions, and a raw material distribution subsystem. This so called “breadboard” tackled these challenges by printing demonstrator parts that serve a dual purpose: providing practical evidence of in-situ manufacturing advantages over Earth-resupply and showcasing manufacturing without build volume constraints.
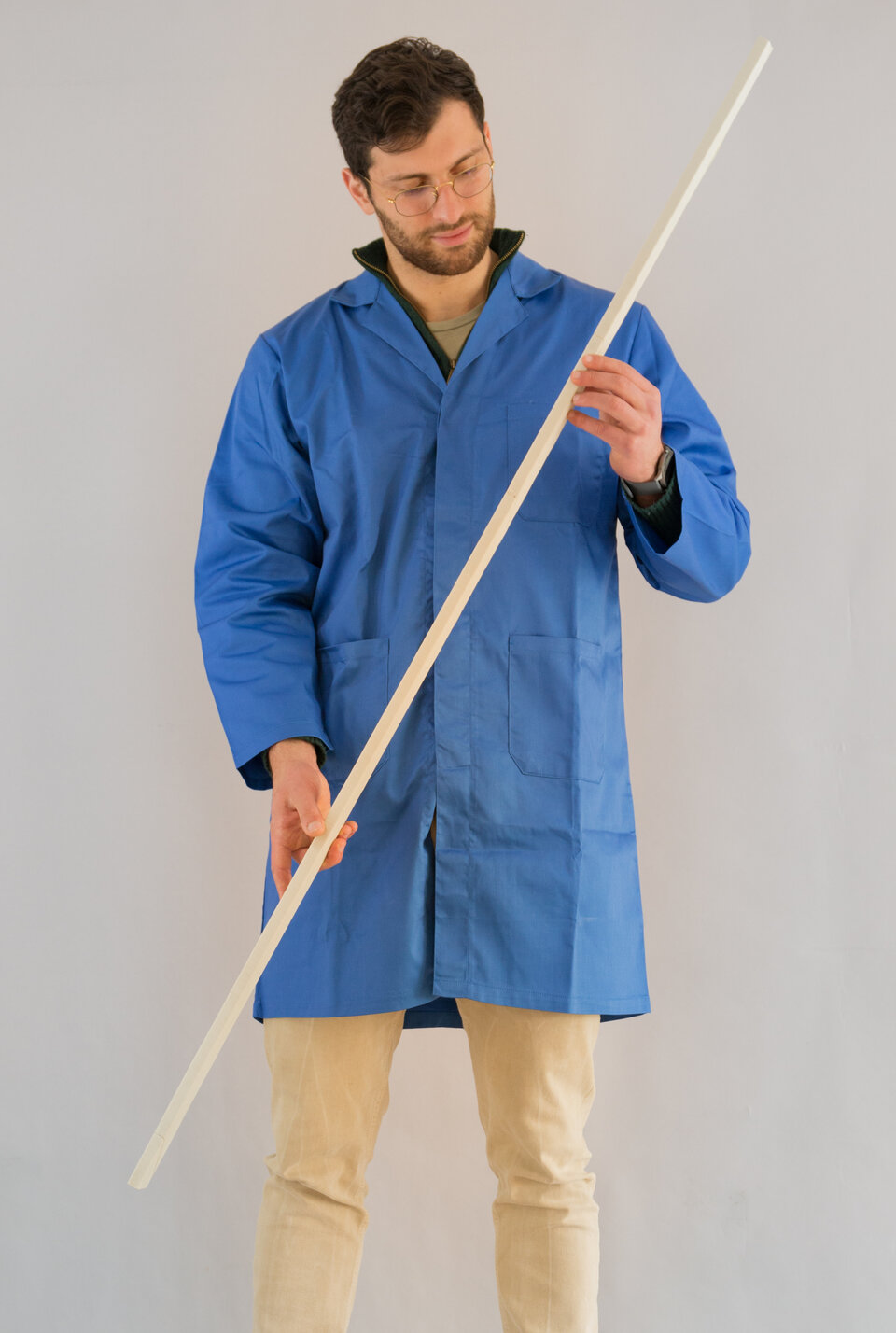
So far an unconfined beam, slider, connector and a socket wrench have all been chosen to illustrate the functionality and flexibility of the IMPERIAL printer's design.
Furthermore, manifolds have been printed in series to provide evidence of the second possible application of the technology demonstrated by the IMPERIAL project: the possibility to print items in batches or series without stop the production process in order to remove the samples from the print bed.
The collaborative effort behind this groundbreaking and cutting-edge project involved a consortium led by OHB System AG in Germany as prime contractor, with Azimut Space in Germany, Athlone Institute of Technology in the Republic of Ireland, and BEEVERYCREATIVE in Portugal playing pivotal roles in developing the 3D printer. The successful completion of the ground-based prototype sets the stage for the next critical phase: testing the IMPERIAL printer in the microgravity environment of the International Space Station (ISS) or onboard alternatives microgravity platforms such us the ESA Space Rider. While the technology is mature enough to undertake these trials, nothing is planned as of yet. The breadboard, or prototype, for the printer has been meticulously designed for integration into the European Drawer Rack Mark 2 (EDR MKII) facility aboard the ISS, ensuring compliance with essential resources such as power, cooling, and, crucially, dimensions.
Further GSTP activities related to Advanced Manufacturing at OHB
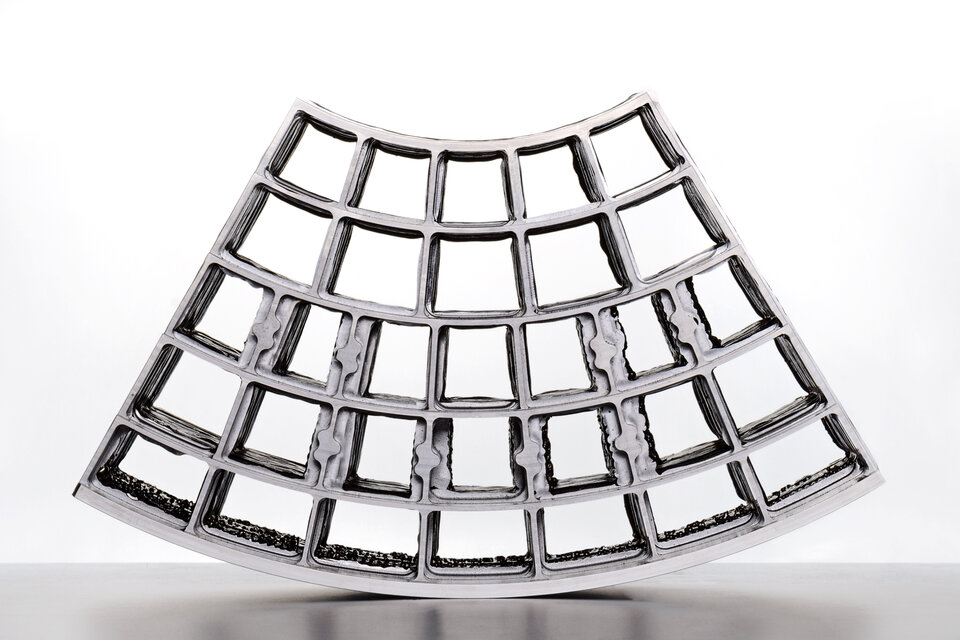
As part of its commitment to advancing space technologies, the General Support Technology Programme (GSTP) is engaged in a series of innovative activities in the realm of advanced manufacturing, not least those part of its Advanced Manufacturing framework. One notable GSTP project, developed in synergy with Dr. Marco Mulser and his team at OHB System AG as well as external partners, involves the maturation of Additive Manufacturing technologies. Within the project, OHB matured the workflow for the design and verification of the quality of AM space applications. Three different parts of different complexity levels were developed. One of the highlights is a Reaction Wheel Bracket made of titanium. Manufactured using Laser Powder Bed Fusion (L-PBF), this advanced manufacturing technique results in a 20% mass reduction compared to the original precision-machined design. The design is used as a baseline to develop an integral component for CO2M satellites which is part of the upcoming Copernicus Sentinel Expansion mission. Another interesting use case is the Integrated Twin-Mirror from within the spectrometer of the Fluorescence Explorer mission (FLEX) instrument. Leveraging advanced manufacturing techniques, the developed AM design achieves a remarkable 45% mass reduction while substantially improving the natural frequency and minimizing stress concentrations for all relevant load cases. A significant reduction in Surface Form Error (SFE) was achieved which is a relevant factor for the instrument’s performance that could only be obtained through the applied innovative manufacturing technology.