20 years of ESA’s Concurrent Design Facility: an oral history
It looks like a flight control room, on the upper floor laboratory corridor of ESA's ESTEC technical heart in the Netherlands: interlinked console are ranged in front of a 6-m long multimedia wall, to host representatives of all space mission disciplines. Except ESA’s Concurrent Design Facility is not a place to steer satellites, but to create them.
Teams of experts gather here to perform ‘pre-Phase A’ studies of proposed future missions, rapidly establishing their initial technical, programmatic and economic feasibility ahead of industrial development.
The CDF has performed more than 250 studies to date, their subjects ranging from CubeSats to Moon bases, system of systems to space telescopes, even audacious probes to the outer planets – along with the very first iterations of numerous ESA missions that have gone on to fly. The CDF is now into its 20th year of operations.
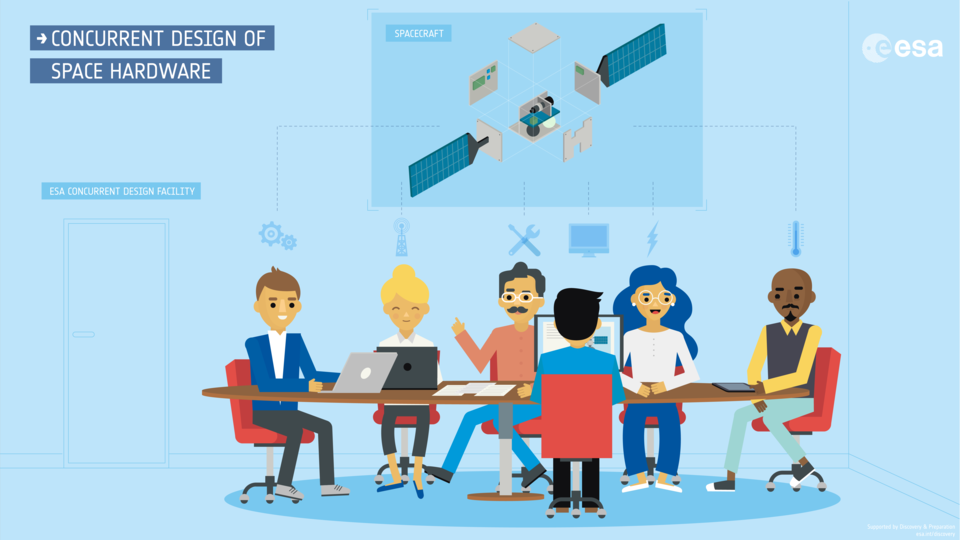
Come together
Massimo Bandecchi, CDF Founder: “Concurrent engineering involves bringing together all necessary experts into a single room to work together in real time. Their collaboration is based on a shared software model of the mission. This model’s configuration is updated as any subsystem alteration is made, showing the system-level impacts of each update to everyone at once.
“It takes a switch in mindset to work this way: participants need to be willing to present ideas that are not yet fully mature, and to confirm and justify their decisions to the other domain experts there with them. With all disciplines contributing at the same time and place, we tackle problems from all points of view, to turn a naturally sequential process into something more ‘concurrent’. The study proceeds on a spiral basis, going around the subsystems until a workable solution is finalised.”
Ilaria Roma, CDF Study Leader: “A single CDF session is four hours long, with two sessions per week. Depending on the subject of the study there might be 25 to 35 people in the room from all different disciplines. It can be quite draining, but exciting at the same time, because there are always challenges arising. As a team leader, it’s like leading an orchestra, to sustain good communication, guide the process and keep it moving toward finding solutions. Depending on the subject, a study might last from four to eight weeks.”
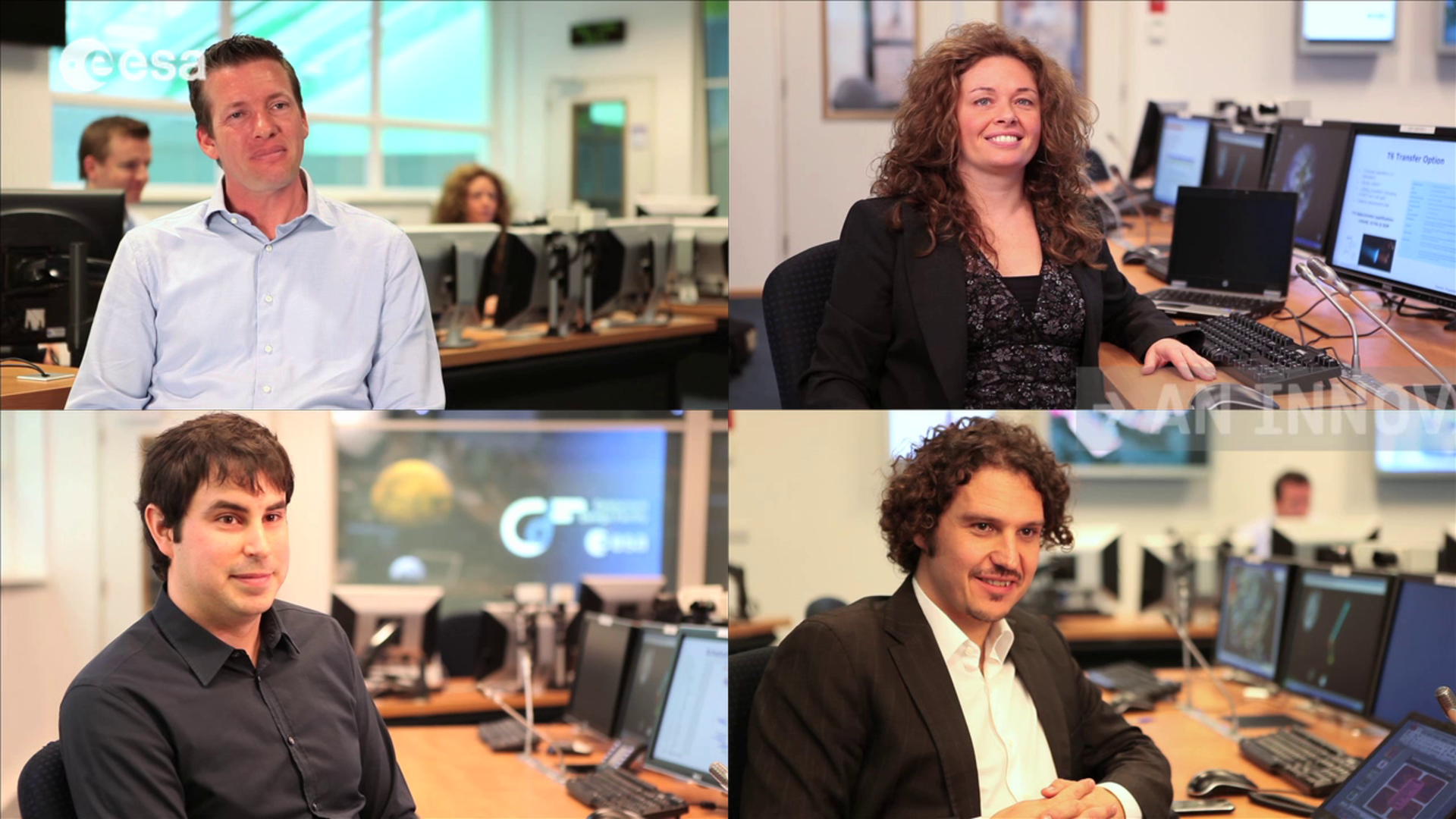
Access the video
Andrew Pickering, CDF Technical Writer: “By contrast traditional mission design is an ‘over-the-fence’ type process, where one domain team – mission analysis for instance – starts work based on the initial mission requirements, then throws it over the fence to the next subsystem team, such as propulsion, passing it in turn to the next.”
Franco Ongaro, Director of Technical and Engineering: “After several months a classical pre-Phase A report is put together, and it’s a good report, but all the detailed working out for the various inputs has been done on the computers of the individual specialists in their own offices. Once the studies are done the experts clean up their computers as they wait for the next study to come along and all that work gets lost for good.”
Andrew: “Of course a change to one subsystem has knock-on implications for the rest… If the payload expert says we need three kilowatts of power then that dictates a minimum size of solar arrays, influencing the overall mission size and structure, and eventually the choice of launcher, based on the configuration you can fit inside a given launch fairing. Or the telecom expert requests the transmission of so much data in a day, requiring this much on-board data storage and demanding a steerable, high gain antenna, which affects the configuration, as well as the demands on the ground segment side. The mission design can shift enormously as it is thrown between these various teams, and accommodating all this in the traditional manner takes much longer than the CDF’s concurrent approach – months rather than weeks.”

Getting started
Franco: “In the late 1990s there were a few people working in-house on proto-concurrent engineering work – notably Massimo Bandecchi. In addition, I [as then head of ESA’s General Studies Programme, now Discovery & Preparation] was invited to JPL to see the work of Team X, a group dedicated to this kind of mission study with everything happening on a single server, capturing all the computation.”
Massimo: “The very first concurrent engineering study I worked on – not that we knew it was called that then – was born of necessity. We had six months to put together a mission called TeamSat, due to fly on Ariane 5’s return to flight following the Cluster explosion in 1996. The original plan was simply to launch a ballast mass, an aluminum cylinder filled with concrete, but to assuage fears over Ariane 5’s reliability the idea was to fly something meaningful. There was no time to make contracts with industry; TeamSat was built entirely in-house. Work began in April 1997 and the rocket launched that October. The second piece of the puzzle was the proposed Euromoon mission, led by ESA astronaut Wubbo Ockels, which was an ambitious mission to the lunar South Pole taking an unconventional approach to design, harnessing a computer network for concurrent engineering. When Euromoon failed to find further support Franco suggested applying the same approach to future GSP studies. We actually tried to lay claim to the same computers Euromoon had used – but by then they were gone.”
Franco: “The final impetus was the then ESA Director General, Antonio Rodotà, asking me to organise a pre-Phase A study for a small satellite. CESAR (Central European Satellite for Advance Research) was a diplomatic gesture for central European candidates to join ESA. It had to be a serious study, but wasn’t part of any established programme, sponsored through the GSP. CESAR was an ideal case to try the concurrent approach, but overall the response wasn’t enthusiastic – except for Massimo. He was the only one who stood up and said ‘let’s do it!’ He went on a fact-finding visit to Team X in JPL, and when he came back he went out to find the appropriate equipment.”
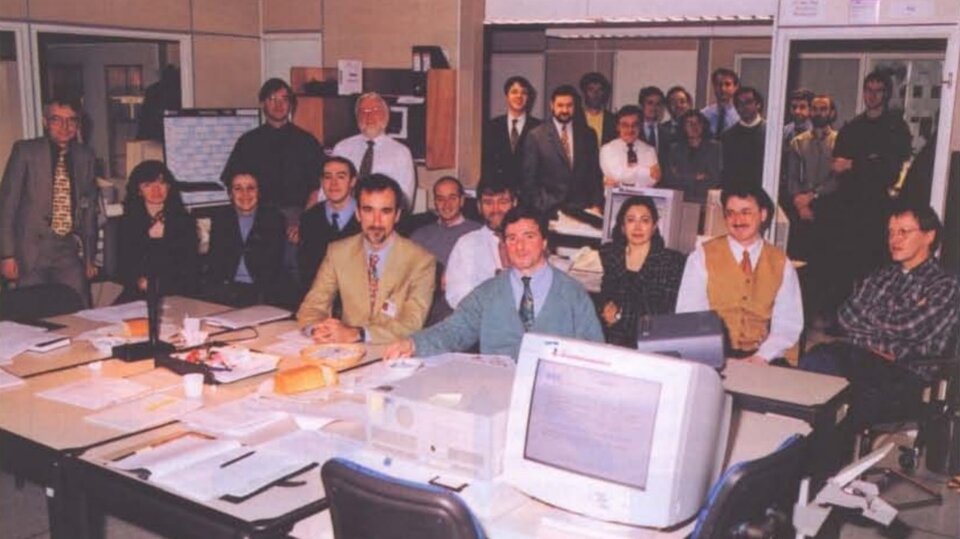
Massimo: “In autumn 1998 we filled the old ESTEC mainframe room with computers, printers, tables, chairs and screens, then gathered the team to start work. The first name we gave the facility had the same name as CESAR – the Concurrent Engineering Setup for Advanced Results – but our Director didn’t like using the name of a person, so it became the CDF instead.”
Andrew: “In those days Microsoft Excel was the basis of our central repository for each study. Today we use an ESA-created, open source Open Concurrent Design Tool which uses the ESA standard we developed for concurrent engineering – ECSS 10-25A – allowing us to transfer data between any compliant design centre of other space agencies or companies. Our standard is specifically for space, although there are other civilian standard for designing ships, aircraft or whatever – concurrent engineering is not purely for space but applicable to any complex engineering.”
Franco: “The old mainframe room still had a lot of cooling piped in, so we had to wear ski jackets to work there, using old Olivetti computers, whatever Massimo could salvage. Our Directorate hierarchy was maybe little bit anxious that a pre-Phase A study performed in this way would be presented to the DG, so they instituted a thorough check of our results.”
Massimo: “Our study was reviewed by a board of senior managers before delivery. This actually went very well, the board gave their blessing.”
Franco: “The best way to convince people something works is to go ahead and do it. They saw we had come to a very credible design with lots of possible configurations and solid decisions, and the DG was happy. Shortly after that Roger Bonnet, the then Director of Science, asked us to perform a quartet of mission studies in a very short time. Science was hooked, for a start – and the rest is history.”

Coming in from the cold
Robin Biesbroek, CDF Senior Study Leader: “Massimo asked me to join him, initially for trajectory analysis, and the first study I worked on was Solar Orbiter. It’s a nice feeling all these years on to see it about to launch – it’s not the same mission exactly, but it’s not so far different either. We were in the same super-cold mainframe room for these four science studies, then moved to a permanent place inside a prefabricated building – ‘the barracks’ – for the next few years.”
Massimo: “It took about six studies to develop the basic methodology, progressing to become more systematic, subsequently establishing our European Cooperation for Space Standardization working standard. We’ve kept busy; some ESA Directorates use the CDF more than others, but all use it at one time or other. Some were concerned it puts the Directorate of Technology, Engineering and Quality in the driving seat of their mission development, but it’s more about giving the customer a way of accessing all the expertise they need, in real time – giving added control, really.”
Robin: “Working in the barracks was an exciting time. We were working on parts of ESA’s Aurora Programme, the human and robotic exploration of our Solar System. ExoMars came out of that of course; we were also looking at things like Moon bases, which widened the amount of experts involved. For the first time we had to consider factors like human logistics in our designs – getting sufficient food to the lunar surface.”
Massimo: “Then in 2008 the CDF was moved to our new purpose-built suite, given pride of place in the new laboratory building.”
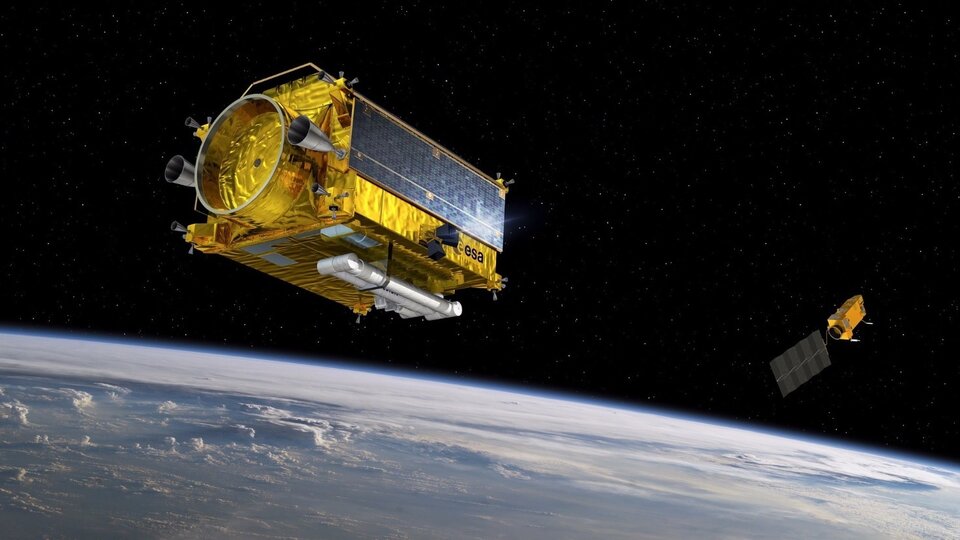
Robin: “In the last decade our set of clients has gone on growing. For instance, Clean Space gave us quite a number of requests, including a ‘cradle to cradle’ study to minimise a space mission’s ecological footprint. The result wasn’t necessarily more complex or expensive, just by making informed choices in terms of materials and orbits we could already make a difference. We also provided system engineering support; for the e.Deorbit mission we tried out model-based system engineering: the entire satellite design process was model-based, rather than requiring standard paper documents. It really made a difference: we could see places where requirements were missing or overlapping, and slashed the documentation needed.”
Massimo: “Team X, our inspiration, came here to find out how we were working. Compared to them we’ve focused more on promotion, standardisation and passing on tools to our partners – about 40 centres have been set up on the CDF model, most European national space agencies have one. JPL have taken less of an interest in this side, perhaps because they function as a mission prime in the US, in competition with other primes.”
Franco: “We had some of the guys at JPL commenting that some of our earlier reports look better than theirs, which was a big compliment from the masters!”
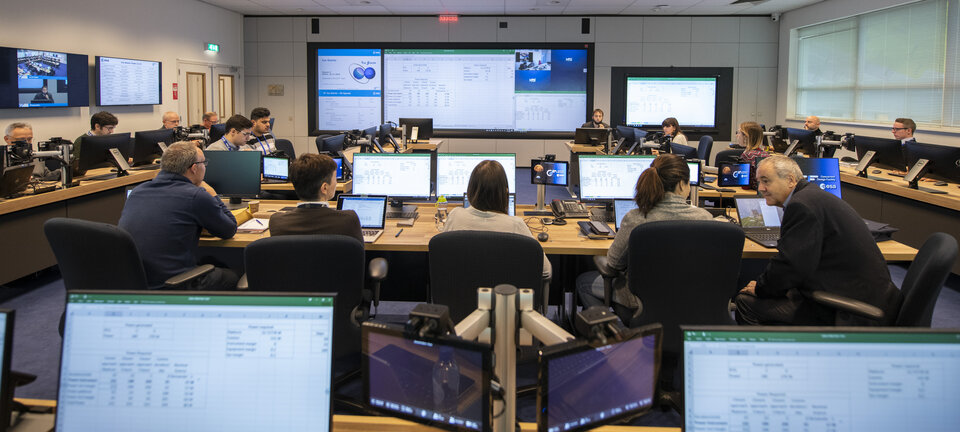
Coming next
Andrew: “We’ve built up a pool of knowledge and expertise for certain destinations; any time we’re given a study for a particular planet we can apply lessons learned from previous studies. And it goes on growing: we perform between 10 to 15 studies per year, plus a number of project reviews and mini-studies with a reduced number of participants, and student training – such as support for the Masters in Space Exploration programme and ESA Education’s Concurrent Engineering Challenge.”
Ilaria: “Concurrent engineering is a human process; sometimes there are fights. Compromise is the golden rule, and the best way to achieve it is to show the facts, and resolve trade-offs via a plenary debate. Sometimes we have to tell customers the mission is not possible in the way they want, but we always find and propose alternative ways forward, maybe less ambitious but still of interest.”
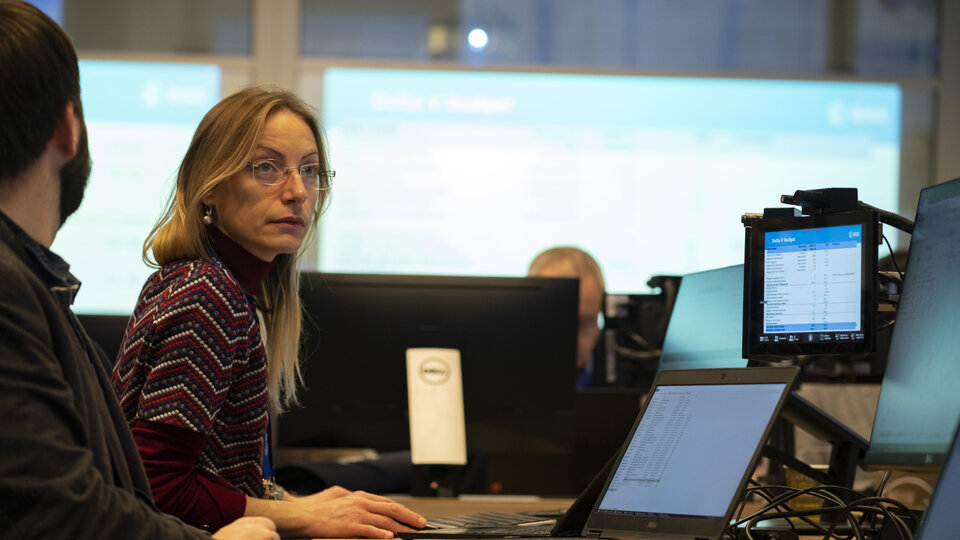
Robin: “How has it changed? Our established rules how to do concurrent engineering are pretty much the same, but we have better ways to share data and calculations now, plus ancillary tools like a 3D printer. That comes in useful sometimes, in the case of CubeSats we can print the spacecraft actual size, to actually see how everything would slot together. One thing we’re looking into in the near future is to embed augmented reality into the process, to really view the mission in the operational environment in space it is destined for.”
Ilaria: “The CDF’s experience with model-based design helped to inspire ESA’s new Design 2 Produce initiative (D2P), which involves expanding the same approach all the way through to manufacturing and testing.
“In the D2P vision, all the engineering data coming from requirements, design, simulation, embedded sensors will be based around the same digital model – the same single reference source, in support and maybe one day replacing today’s documentation – to make the design and development process soother and faster, identify anomalies early, perform detailed simulations in place of costly physical testing and train operators, as well as harvest data throughout the production cycle to feed back into follow-on design phases. It’s a big change in mind-set and will require everybody together to change the way we work and concurrent engineering will be a key factor: a big challenge for CDF and for ESA.”