Ariane 5 bulkhead design assessed for Airbus airliners
An adapted version of a composite bulkhead that safeguards satellites during their ascent on the ESA-developed Ariane 5 launch vehicle has been tested for service aboard single aisle Airbus aircraft. Fitted in the rear tail cone, it would serve as a firewall to protect passengers in the event of the rear auxiliary power unit engine catching fire or the main cabin pressure bulkhead rupturing.
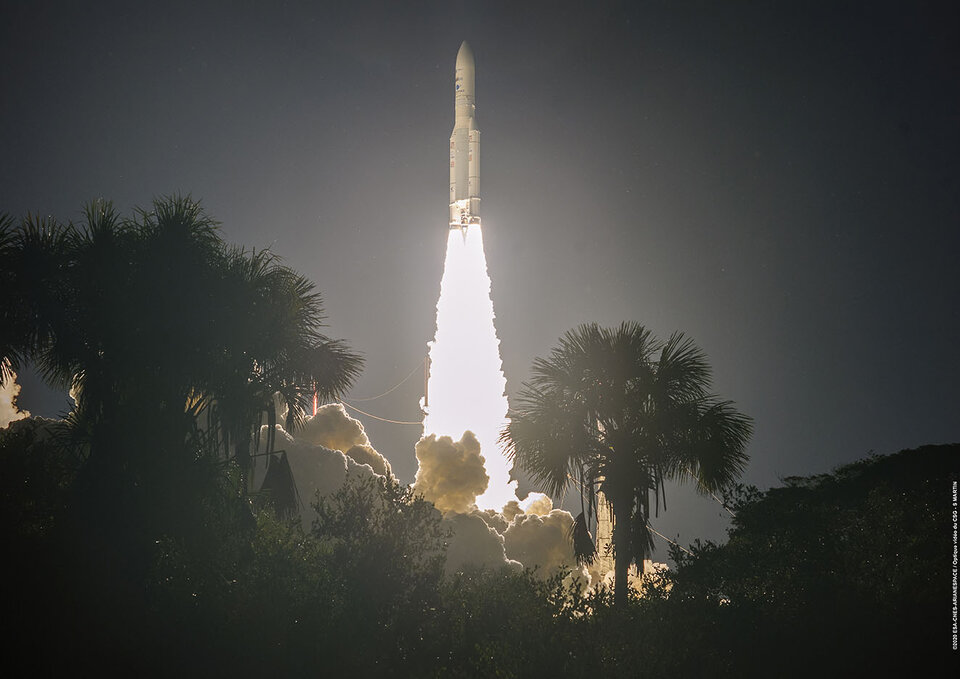
Spanish structural specialist CITD collaborated in the design of the Ariane 5 bulkhead with Airbus Defence and Space Spain and worked with ESA’s Technology Transfer and Patent Office (TTPO) to probe the feasibility of transferring the design from rocket launcher to airliner.
“The task of this bulkhead aboard Ariane 5 is to protect the satellite from the launcher exhaust, dust or overpressure from the launcher stage below it,” explains Marta García Cosío of CITD.
“But the original version was a glass fibre cloth supported by massive aluminium rings and fasteners. It was very complicated to manipulate and integrate, so was seen as an opportunity for improvement. Accordingly we looked into the use of carbon-fibre reinforced polymer, CFRP – although new challenges appeared in turn.”

Strong yet light CFRP is made by casting plastic resin with carbon fibres threaded through it for robustness, following a similar approach to steel-reinforced concrete. It can be moulded into complex rigid shapes, such as the aerodynamic bodies of Formula One automobiles, or the wingtips or noses of many modern aircraft – and the solid rocket motor casings of Europe's Ariane 6.
“We came up with an effective wavy shape to render the flat CFRP bulkhead stiff and self-supporting, as well as pressure resistant,” adds Marta. “Then it flew for the first time aboard Ariane 5 in 2020 and is now the baseline for this launcher, as well as the upcoming Ariane 6.”
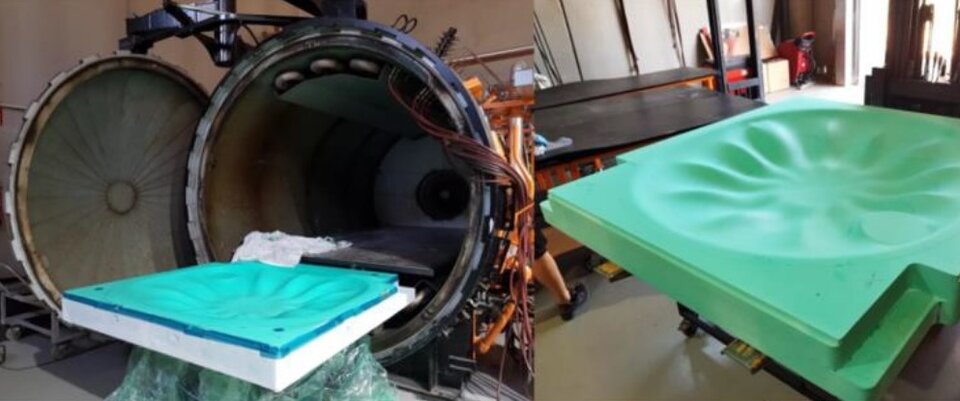
But the CITD team thought that the ‘crumpled petal’ design also had potential for wider use, Marta explains: “We already had contacts with Airbus, and it seemed obvious to us this would be a good fit for commercial aviation as well. We pushed and pushed then finally, through ESA’s involvement, we got our chance to try.”
CITD worked with TTPO, initially through a Feasibility project, then a follow-up Proof-of-Concept project which culminated in the prototype 2-m diameter bulkhead being successfully tested at Airbus, incorporating critical fuselage interfaces such as fuel and air bleed ducts and fire sensors.
ESA structural engineer Shumit Das advised on the project: “The candidate bulkhead to replace was carefully chosen. We didn’t want to touch the primary bulkheads maintaining pressure in the cabin, instead we chose a secondary aft bulkhead, a firewall that is adjacent to the small gas turbine engine that provides power while the aircraft is on the ground, providing protection in the event of these engines catching fire.
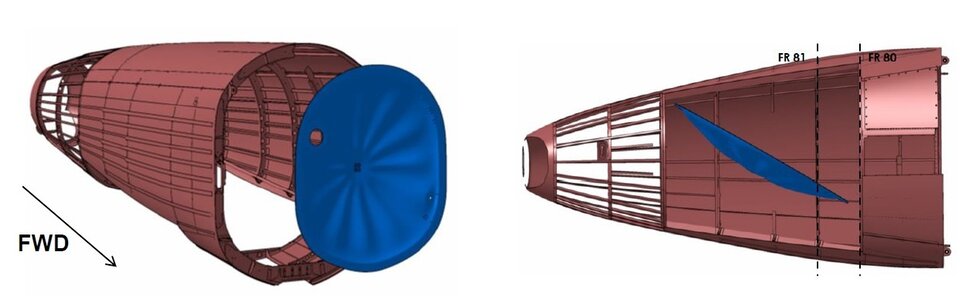
“The current bulkhead is a flat piece of titanium with hundreds of fasteners and stiffeners needed to stop it collapsing – which involves a long process to install. What the project team has done is swap this with a single piece of composite, made to exactly the right shape with all necessary holes for power and fuel conduits, and fire sensors. By saving hours at a time, this could have a big impact when it comes to integrating dozens of aircraft per month.”
The Proof of Concept project was overseen for ESA by Technology Transfer officer Mercedes Sanchez Alvarez: “The fit check by Airbus Spain was the moment of truth. It always takes an effort to replace a legacy part, and if the manufacturing teams involved don’t like our demonstrator, then they won’t be interested in taking it further. The good news is the system installations went well, and CITD is now looking into taking the concept further, at the same time as Airbus is designing its coming generation of aircraft.”
“This new CFRP firewall is a very promising revolutionary structural concept that will be considered for the next generation of aircraft,” states Javier Vazquez from Airbus’s research and technology team.
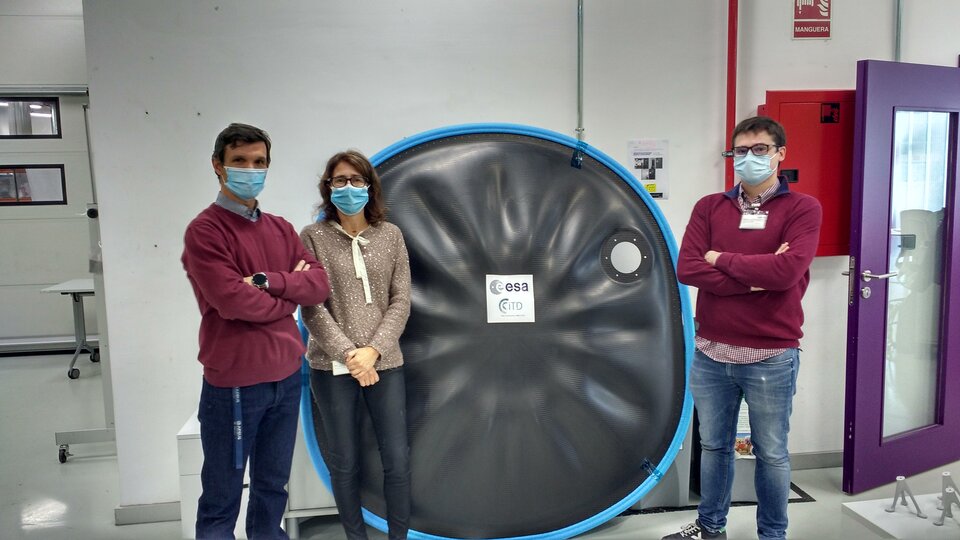
This next step would include overpressure and fire testing, and consideration of manufacturing scale options. The bulkhead demonstrator was cast from automotive grade composite material, for instance rather than the more costly aeronautic grade material.
“We did this to keep costs low, but Airbus said that maybe it is a good idea, and any operational version could be made the same way,” adds Marta. “Because the company is looking into reducing costs as well, and if the existing bulkhead meets all performance requirements, why not?”
Tommaso Ghidini, heading ESA’s Structures, Mechanisms and Materials Division, comments: “This is a great example of the kind of initiative that cuts across disciplines and industry sectors. By selecting just the right shape with the right materials, space engineers can combine form with function, to do more with less for our projects, and pass on enhanced efficiency to terrestrial sectors too.”