From the Moon to Mars, future missions studied by CDF
How would you construct an inflatable base on the Moon? What is the optimal way of providing early warnings of space weather? How would you map in the world in high resolution from geostationary orbit? What would 3D-printed CubeSats look like? Which is the best way to go to Mars? All questions recently asked of ESA’s Concurrent Design Facility – where experts comes together to make preliminary designs of mission proposals and novel technologies.
It looks like a flight control room, on the upper floor laboratory corridor of ESA's ESTEC technical heart in the Netherlands: interlinked consoles are ranged in front of a 6-m long multimedia wall, hosting representatives of all space mission disciplines to work together on shared software models, and slash mission design times from months to weeks.
In more than two decades of operations, ESA’s Concurrent Design Facility (CDF) has performed hundreds of ‘pre-Phase A’ studies of proposed future missions and technologies, including numerous spacecraft that have gone on to fly. Despite continuing COVID-19 restrictions, ESA’s CDF is in the midst of one of its busiest years yet.
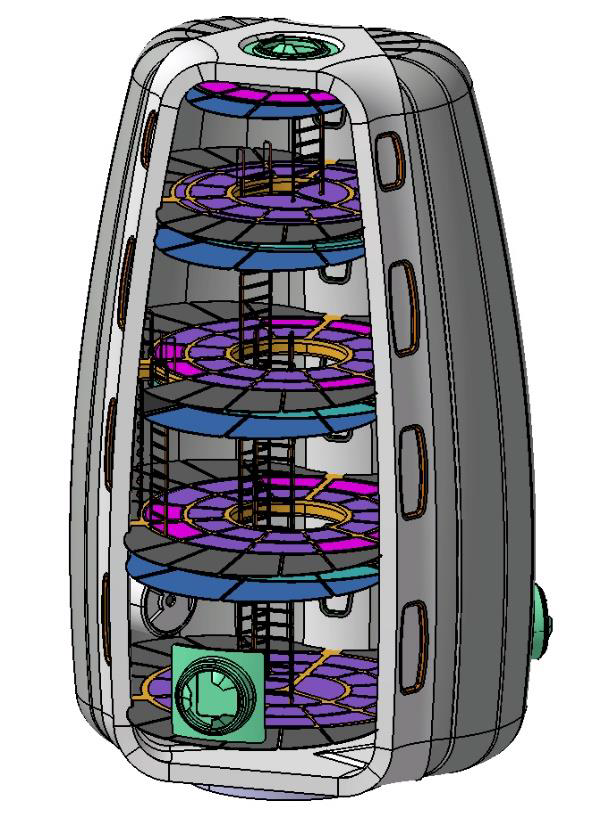
2020 began with a conceptual definition of a lunar habitat module, intended as part of a future international ‘Moon Village’. The study was performed in partnership with the Department of Aeronautics at MIT and US architecture, interior design, engineering and urban planning firm Skidmore, Owings and Merrill (SOM).
Their innovative proposal is an inflatable structural shell technology to be placed on the rim of Shackleton Crater near the lunar South Pole, offering access to near-continuous sunlight and lunar water ice deposits in adjacent ‘cold trap’ craters.
The CDF design team looked into the challenges associated with putting such a design in place, including transport to the site, its erection and commissioning as a safely habitable dwelling. Radiation protection would be an issue throughout its operation, and the team also considered how to make maximum use of lunar resources while working within the habitat’s proposed power requirement of 60kw.
While no solid design solutions were agreed, many requirements were identified, as were a multitude of further investigations.
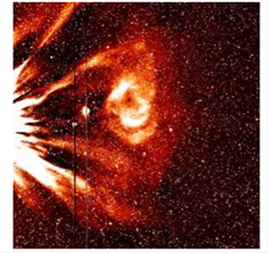
The CDF’s next two studies were performed in parallel: a redesign of the Lagrange space weather mission and a novel Earth Observation telescope mission for geostationary orbit.
Lagrange will be Earth’s first dedicated space weather observatory to warn of potentially harmful turbulence in our parent star. Positioned 150 million km away at Earth-Sun Lagrange point 5, the spacecraft will resemble a referee at a sports game, able to simultaneously observe both the Sun and Earth as well as the space in between.
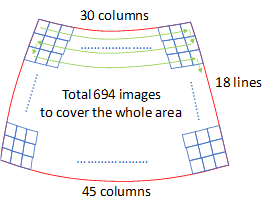
But Lagrange’s original iteration received insufficient support at last year’s Space19+ Ministerial Council, so the CDF study looked into the possibility of achieving mission goals through a minimum configuration within a fixed budget, including splitting the payload between two smaller satellites.
The other study was performed jointly with the Japan Aerospace Exploration Agency, JAXA, considering a ‘Geostationary Observatory’ for disaster and security monitoring of Earth. Operating in geostationary orbit gives the advantage of keeping in the same point of sky relative to the surface, but at a formidable distance of 36 000 km away the challenge is achieving a useful image resolution.

So the study team compared telescope designs of various sizes: a 1.2 m telescope mounted on an existing modified platform and twin 2 m telescopes, one using a traditional monolithic mirror and the other using a segmented mirror, both mounted on a new platform, as well as taking a first look at a larger 4 m design. Various modes of operations were proposed, including close-up ‘carpet mapping’ as well as persistent and video monitoring.
March and April saw a study on ‘Additive Manufacturing Advantages for CubeSats’, undertaken as part of ESA’s Advanced Manufacturing initiative. CubeSats are small, cheap missions built up from standardised 10-cm boxes; the aim was to develop an in-orbit demonstrator CubeSat making maximum use of additive manufacturing, otherwise known as 3D printing.
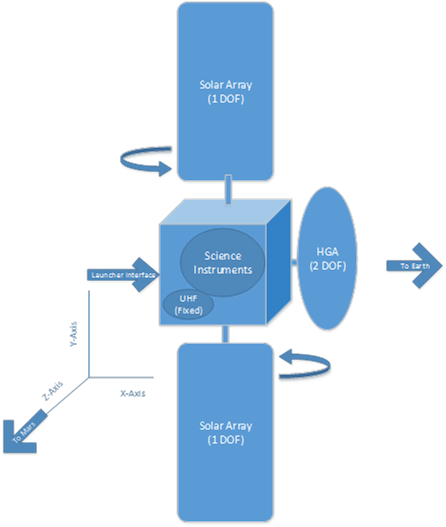
The study considered all aspects of CubeSat design, with its main focus on tanks, filters, thruster components, heat pipes, radiator panels, deployable thermal panels, wave guides and brackets/supports.
Around the same time the CDF performed a 10-session architecture study on potential small missions to Mars to understand whether there was potential in Europe for developing high-value, low-cost Mars missions that could be implemented in parallel or soon after an international Mars Sample Return campaign. Mission scenarios included a constellation of communication satellites to support relay of data from surface assets, a small science orbiter and a network of hard landers/penetrators for meteorology.