Identification of structural components damping characteristics at microvibration level
Programme: | GSTP | Achieved TRL: | 4 |
Reference: | G517-134MS | Closure: | 2016 |
Contractor(s): | HTS GmbH (DE) |
Spacecraft typically contain a number of mechanisms to provide high performance functionality with high reliability. During operation these mechanisms emit low level mechanical disturbances in a considerably wide frequency range, which are transmitted through the entire structure of the spacecraft. A project was initiated to study, measure and model microvibration damping capabilities of typical structural components and interfaces in spacecraft, in addition to the ongoing studies and developments for characterizing and optimizing microvibration sources and receivers.
Objectives
The primary objective of this project was to characterize by test, the damping properties of representative spacecraft structure components and interfaces, including honeycomb panels, bolt interfaces, bonded interfaces and to assess effect of harness on the structural damping. For this characterisation, a dedicated test setup was developed, commissioned and coupled with a comprehensive test campaign, considering different types of vibration excitation and vibration levels. The secondary objective was to simulate the damping by means of finite element models and to prepare a guidance for microvibration modelling in future projects to provide grounds for improvement of structural design for future spacecraft employing vibration sensitive payloads.
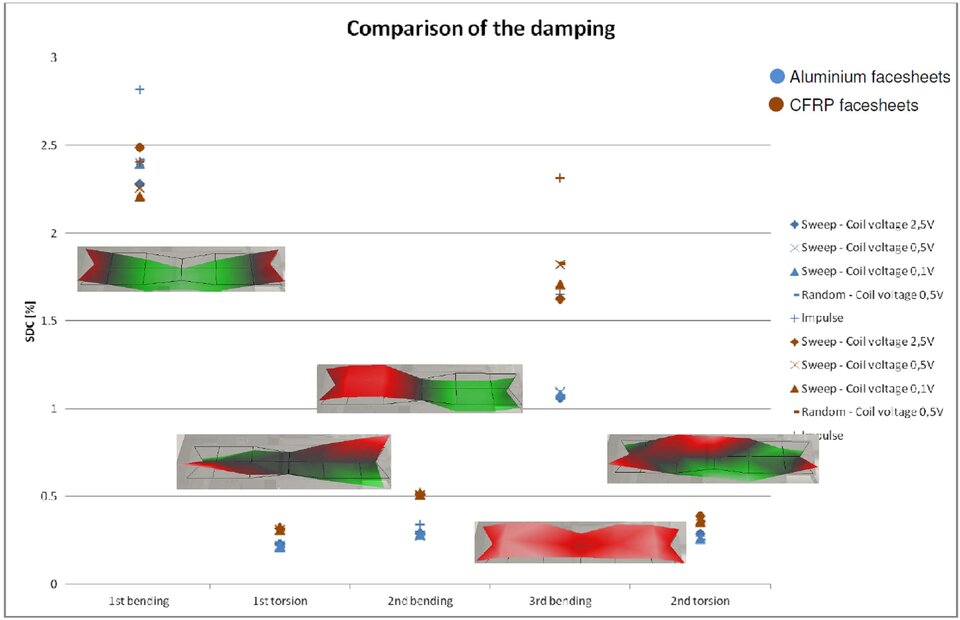
Achievements and status
In order to cover as many as possible structural configurations for the characterization of microvibration damping properties a set of components is defined, which were combined in different ways to achieve several test configurations and test cases. Based on the analysis of the test data the following generic observations are noted:
- Damping values found in literature used for spacecraft structure simulation (typically between 0.1% and 1.0% SDC) could be confirmed for small excitation levels, yet it could be seen that the damping may vary significantly for each mode shape.
- The damping of CFRP panel is typically higher compared to aluminium panels, however this is very case specific and strictly depending on the actual mode shape
- Damping is majorly driven by the mode shape, less by excitation level or type: no clear correlation of excitation level and damping visible, however in specific cases and structural configurations
- Pottings increase damping significantly (roughly one order of magnitude, compared to raw panel), whereat only a slight difference between partly potted and fully potted inserts was observed (partly potted inserts have higher damping, especially at first bending mode)
- Harness leads to non-deterministic vibration behaviour due to numerous local modes which are interacting and disturbing the raw panel modes, effectively leading to significantly increased damping, especially in longitudinal harness direction
Benefits
All programmes where mechanisms are required in the space segment or where microvibrations are mission critical. The findings can be related to the damping mechanisms used for vibration problems in any kind of machinery, especially for lightweight structures, e.g. in aeronautics. An application could be the control of accuracy in microelectronics, e.g. wafer structuring
Next steps
In a next development step, the test setup should be rescaled to consider larger and more complex structural configurations. By using, several laser vibrometers a three dimensional scanning becomes possible. Furthermore, the dynamics and non-linearities induced by harness should be analysed more to detail, by dedicated testing and adequate modelling.