OPS-SAT
ESA’s OPS-SAT mission came to an end during the night of 22—23 May 2024 (CEST).
-------------------
A flying laboratory, ESA's OPS-SAT is the first of its kind, with the sole purpose of testing and validating new techniques in mission control and on-board satellite systems.
OPS-SAT is devoted to demonstrating drastically improved mission control capabilities, that will arise when satellites can fly more powerful on-board computers. The satellite is only 30cm high, but it contains an experimental computer ten times more powerful than any current ESA spacecraft.
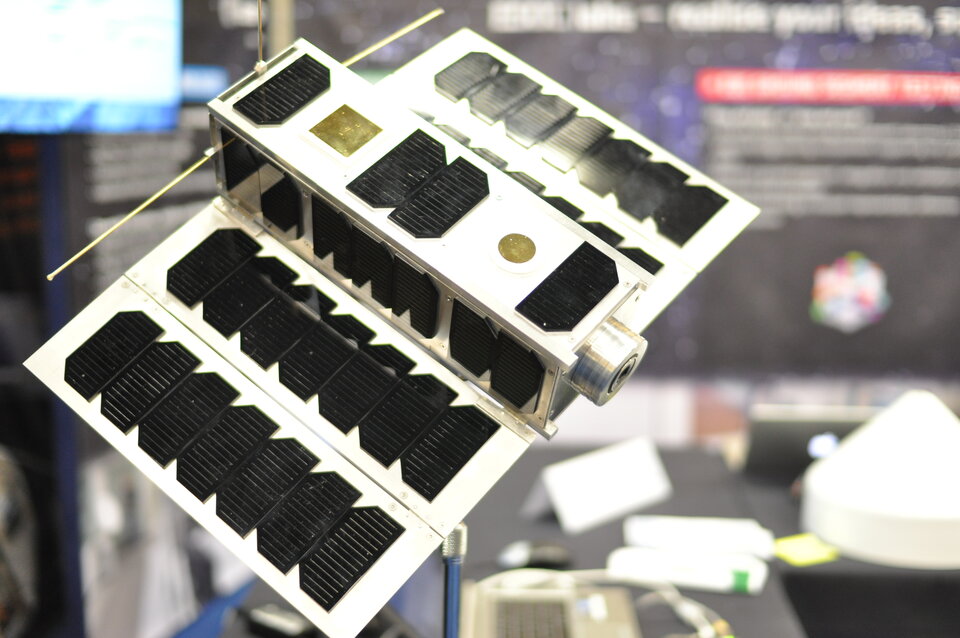
It is very difficult to perform live testing of mission control systems. No-one wants to take any risk with an existing, valuable satellite, so testing new procedures, techniques or systems in orbit is not often possible.
The OPS-SAT solution is to design a low-cost satellite that is rock-solid safe and robust, even if there are any malfunctions due to testing.
The robustness of the basic satellite itself will give ESA flight control teams the confidence they need to upload and try out new, innovative control software submitted by experimenters; the satellite can be pushed to its limits but can always be recovered if something goes wrong.
Achieving this level of performance and safety at a low cost is a challenge. To do this, OPS-SAT combines off-the-shelf subsystems typically used with cubesats, the latest terrestrial microelectronics for the on-board computer and the experience ESA has gained in operating satellites for the last 40 years in keeping missions safe.
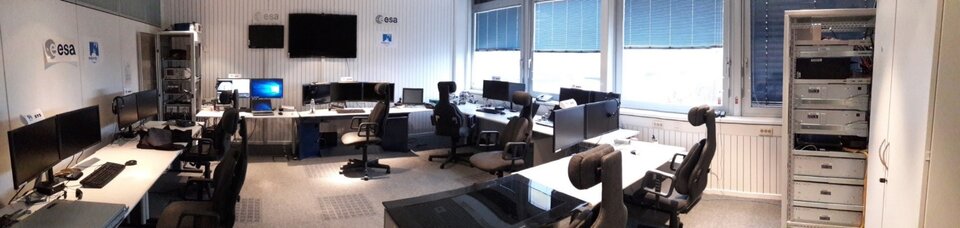
The result is an open, flying 'laboratory' that will be available for in-orbit demonstration of revolutionary new control systems and software that would be too risky to trial on a 'real' satellite. Over 100 companies and institutions from 17 European countries have registered experimental proposals to fly on OPS-SAT.
The in-orbit laboratory will offer a range of resources, including processors, field-programmable gate arrays (FPGAs), cameras, and an attitude determination and control system, all of which experimenters will be able to exploit for demonstrating new mission and operations concepts.
The OPS-SAT architecture consists of two major parts. The first is the OPS-SAT 'bus', which provides the necessary infrastructure to operate the second part, the payload. However, in this case, once the payload is running it can take over control of the entire satellite while the bus monitors and is ready to take control back at any moment.
The payload
Processing platform
The heart of the OPS-SAT satellite payload is the processing platform, which is responsible for providing a reconfigurable environment able to fulfil the objectives of each experiment. The processing platform runs Linux, as the operating system consists of a flexible and reconfigurable framework, featuring sophisticated processing capabilities, interfaces, memory integrity and reconfigurable logic.
The platform consists of an 'Altera Cyclone V SoC' with an ARM dual-core Cortex-A9 MPCore and a Cyclone V FPGA. OPS-SAT experimenters will provide bootable images for this processing platform. These images will undergo certain pre-checks before loading to the spacecraft. Power consumption and temperature of the processing core will also be monitored by the on-board computer to provide additional safety mechanisms.
Fine Attitude Determination Control System (ADCS)
An integrated fine ADCS will provide the experimenters with access to sensors and actuators as well as integrated attitude control functionality. It consists of gyros, accelerometers, magnetometers, reaction wheels, three magnetorquers and a Star Tracker.
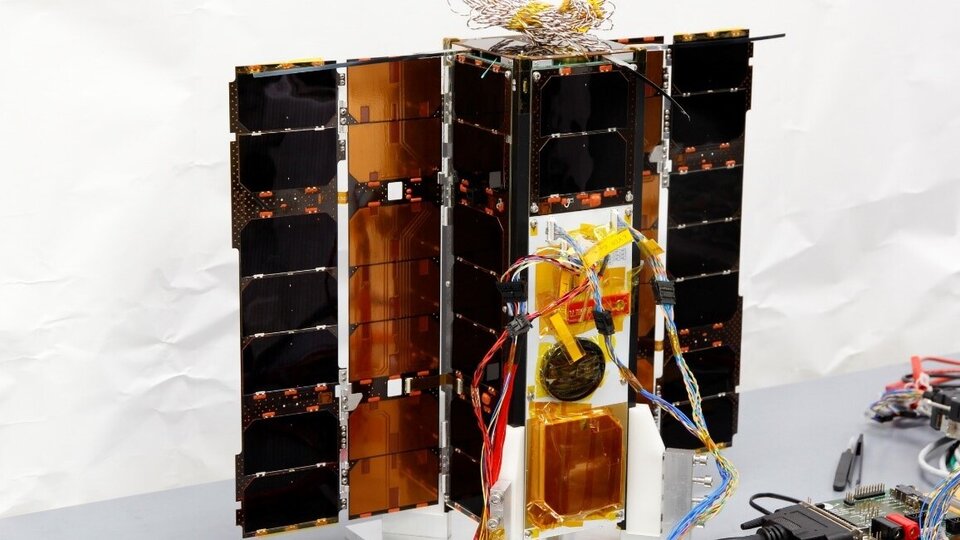
Global Positioning System (GPS) receiver
A GPS module is provided, so experimenters can have access to positioning data and time information.
S-Band Transponder
For high data-rate communications a CCSDS-compatible S-band communication link, acting as the main link for data communications and TM/TC with ESA ground stations, is provided. It will provide uplink speeds of up to 256 kbit/s and downlink speeds of up to 1 Mbit/s. The S-band link will be used to upload experimenter’s’ software and download results of on-board experiments.
X-Band transmitter
An X-band transmitter with high data-rate communications of up to 50 Mbit/s.
Camera
A high-resolution camera which can provide a ground resolution of up to 80m x 80m per pixel.
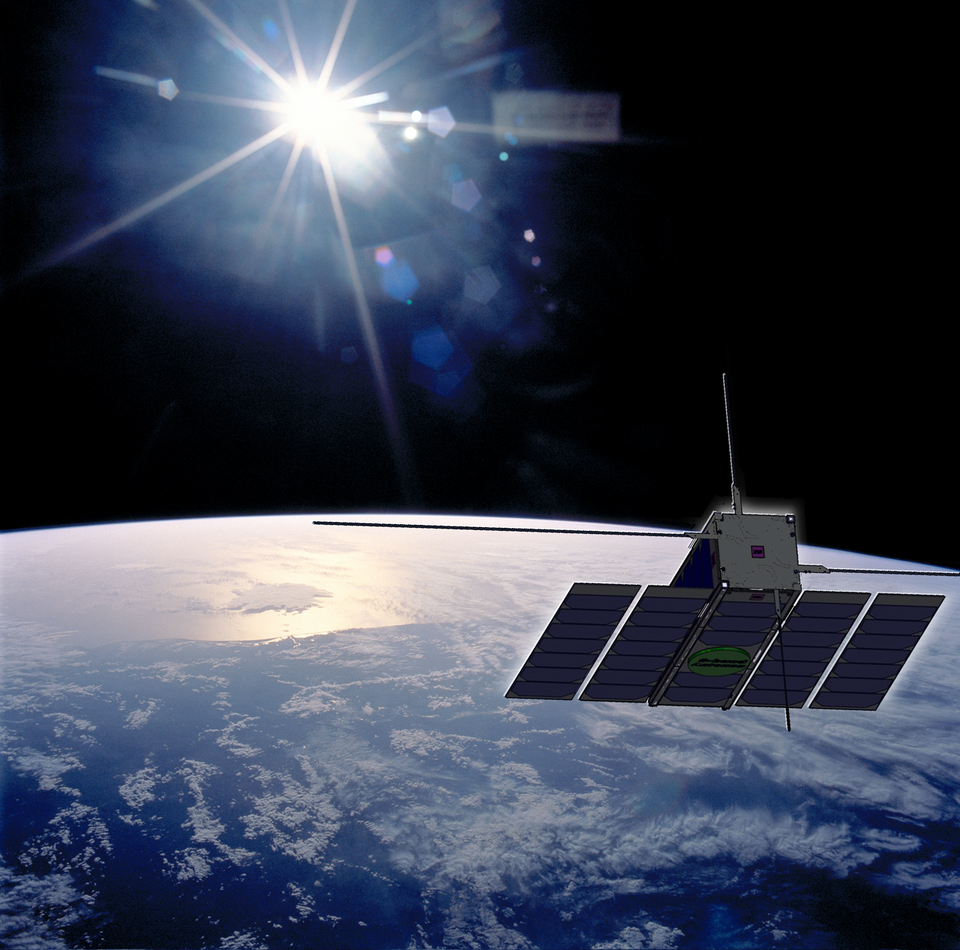
Optical uplink
An optical receiver will be provided that can receive commands from a laser ranging station on Earth. An uplink rate of 2 kbps is expected.
Software defined radio
A software-defined radio front end will be provided, connected to one of the pair of diploes in the UHF antenna. The results of this experiment will be made available on the processing core for further processing by experimenters, for example providing a flying spectrum analyser.
Interfaces
Experimenters will be able to communicate with their flying experiments in various ways, ranging from offline file transfer only, to receiving and sending space packets in realtime with a brand new CCSDS protocol (MO services) over the internet.
Project status

The project is funded by the ESA General Support Technology Programme. This project kicked off on 4 February 2015 with the prime contractor, the Technische Universität Graz, and subcontractors.
Launch took place on 18 December, 2019, when OPS-SAT was injected into a circular, polar orbit at 515 km altitude. The spacecraft was launched as a 'secondary payload' along with the CHEOPS planet-characterising mission. OPS-SAT is now controlled from the dedicated SMILE control room at ESOC.