Secrets of pearl harnessed for stronger space structures
Pearls and seashells are made from the same basic stuff as easily crushed chalk – humble calcium carbonate – so why are they so much tougher? Researchers are taking design tips from the micro-structure of these naturally formed materials to produce stronger, more fracture-resistant ceramics for future space missions.

“You can think of nature as a vast laboratory working across lengthy timescales to develop composites of interest to various forms of life,” comments Eduardo Saiz, Chair of Ceramics at Imperial College in the UK.
“Now the actual materials that nature has available to work with is quite limited – basically carbonates and silicates – but the process of evolution refines them to be as robust as they possibly can be. Our idea is to take inspiration from the outputs of this natural process and apply the same approach to materials that are already quite tough, to make them even tougher.”

Imperial College is working with ESA on this topic, having won a contest on ‘bio-inspired’ materials through the Agency’s Technology Development Element, working on promising new technologies for space.

The focus on their project is on nacre, otherwise known as Mother-of-Pearl, the material that pearls and inner seashell layers are made from. Nacre is synthesised by oysters and mussels to surround pieces of grit and other unwanted irritants, or by molluscs in the form of a protective shell.
“These pearls and shells are mainly composed from calcium carbonate, which is the same material making up chalk. However these items end up much stronger than what is typically an easily crushable material. The reason why is found in their micro-structure: nacre is based on a brick-and-mortar design, with platelets of calcium carbonate bound in an elastic bio-polymer mortar such as chitin and various proteins.”

Individually these platelets are small and brittle – at half a thousandth of a milllimetre in thickness, they are close to the wavelength of visible light, leading to nacre’s distinct iridescent appearance. However collectively, the interlocking platelets embedded in their elastic mortar lend nacre high strength and cohesion, while inhibiting the propagation of cracks.
“This is interesting for space in terms of ceramics in particular,” explains ESA materials engineer Malgorzata Holynska. “We employ ceramics to produce spacecraft parts such as heat shields, optical benches and structural parts, but they are more brittle than we would like, so we are looking into how we can improve them.”

To serve as bricks, the project team has focused on silicon carbide (SiC). A compound of silicon and carbon, SiC was first synthesised in Victorian times, in an attempt to make artificial diamonds. This resulted in one of the hardest known materials, since used to make cutting tools, high-performance brakes and even bulletproof vests.
SiC has proved valuable in the space sector as well. Its high stiffness combined with its relative insensitivity to temperature changes means that the ceramic has been employed for space telescope mirrors and optical benches, as well as structural items. But at the same time SiC’s brittle nature means it can sustain serious damage from knocks.

Prof. Saiz adds: “The idea is to improve upon the performance of SiC by arranging our material into a nacre-style brick-and-mortar structure, with potentially the mortar including a temperature resistant glass. The result would be a further toughened composite. Depending on how the composite is laid down, we could also add anisotropic characteristics, to make it stronger along particular directions in the material.”
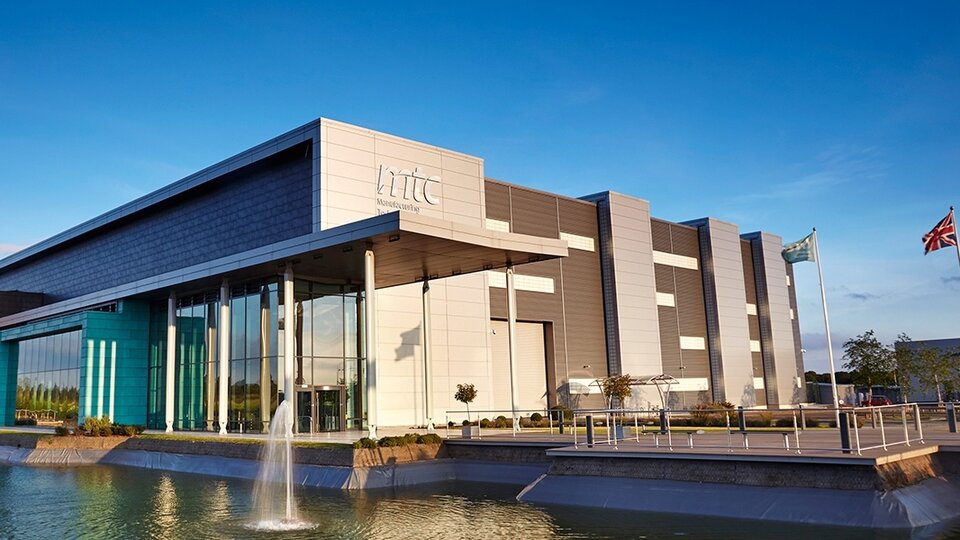
“The challenge is that nature works from the bottom up, while we are working from the top down. We have to see if we can harness existing production methods to replicate the key structural features we need, down to the necessary scale. And can we do so in a way that is relevant and practical for the kind of materials required for space missions??”
The team is looking into a range of production options, including additive manufacturing and also ‘freeze casting’: this involves the directional freezing of ceramic suspensions in water, employed in turn to build layered inorganic scaffolds.
The project began last year, with samples synthesised at Imperial College’s laboratory and tested at Azimut Space in Germany, with the Manufacturing Technology Centre at Coventry in the UK looking into scaling up production processes.